离合器压盘淬火:超高频淬火设备热处理工艺选择与质量保障
作者:
小编
点击数:
发布日期: 2025-07-07
离合器压盘作为汽车传动系统的核心部件,需承受高频摩擦与交变载荷,其表面硬度(通常要求 HRC38-45)与平面度直接影响离合器的接合平顺性和使用寿命。超高频淬火机在压盘热处理中虽能实现局部硬化,但人工操作与全自动高频淬火机床的质量稳定性差异显著,尤其对汽车用压盘,机床淬火是更可靠的选择。
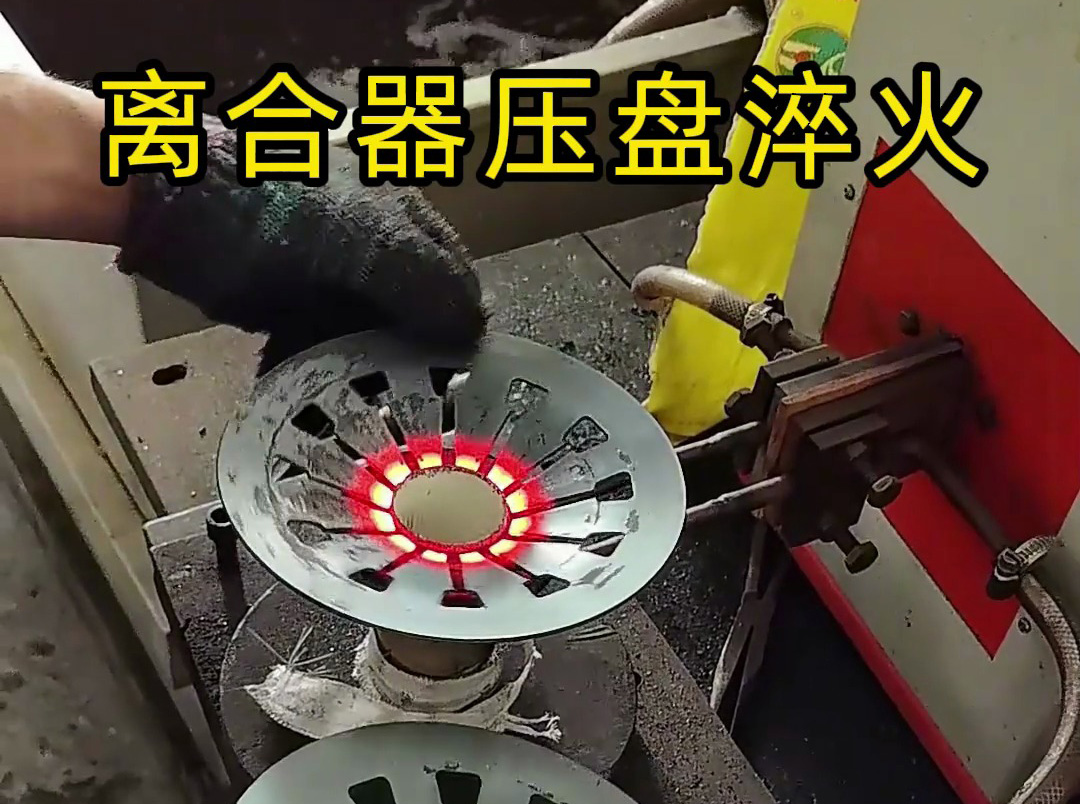
离合器压盘(多为灰铸铁或合金铸铁材质)的淬火重点是摩擦工作面:
- 硬度均匀性:整个摩擦面的硬度偏差需≤±2HRC,避免局部过硬导致的磨损不均或过软导致的早期失效;
- 变形控制:淬火后平面度误差需≤0.1mm/m,否则会造成离合器打滑、异响;
- 淬硬层深度:通常要求 1.5-2.5mm,过深会降低压盘韧性(易断裂),过浅则耐磨性不足。
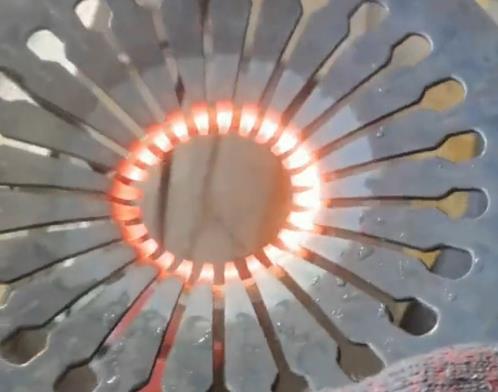
对比项 | 人工超高频淬火 | 全自动高频淬火机床 |
---|
加热精度 | 依赖人工经验控制加热时间 / 温度,易因操作节奏差异导致局部过热或欠热 | 红外测温 + PLC 程序控温(±5℃),加热均匀性误差≤3% |
定位一致性 | 人工手持线圈对准摩擦面,易因偏移导致边缘漏淬或过度加热 | 机械臂自动定位,线圈与压盘同轴度误差≤0.05mm |
冷却稳定性 | 人工控制冷却时机,易因延迟导致硬度不足 | 加热完成后 0.5 秒内自动启动喷雾冷却(压力恒定 0.3MPa) |
批量一致性 | 同一批次硬度偏差可达 ±5HRC,合格率约 80% | 偏差≤±1.5HRC,合格率≥99% |
某汽车零部件厂的数据显示:人工淬火的压盘在台架试验中,平均使用寿命约 5 万公里;而全自动机床淬火的压盘寿命达 15 万公里以上,且无因淬火质量导致的早期故障。
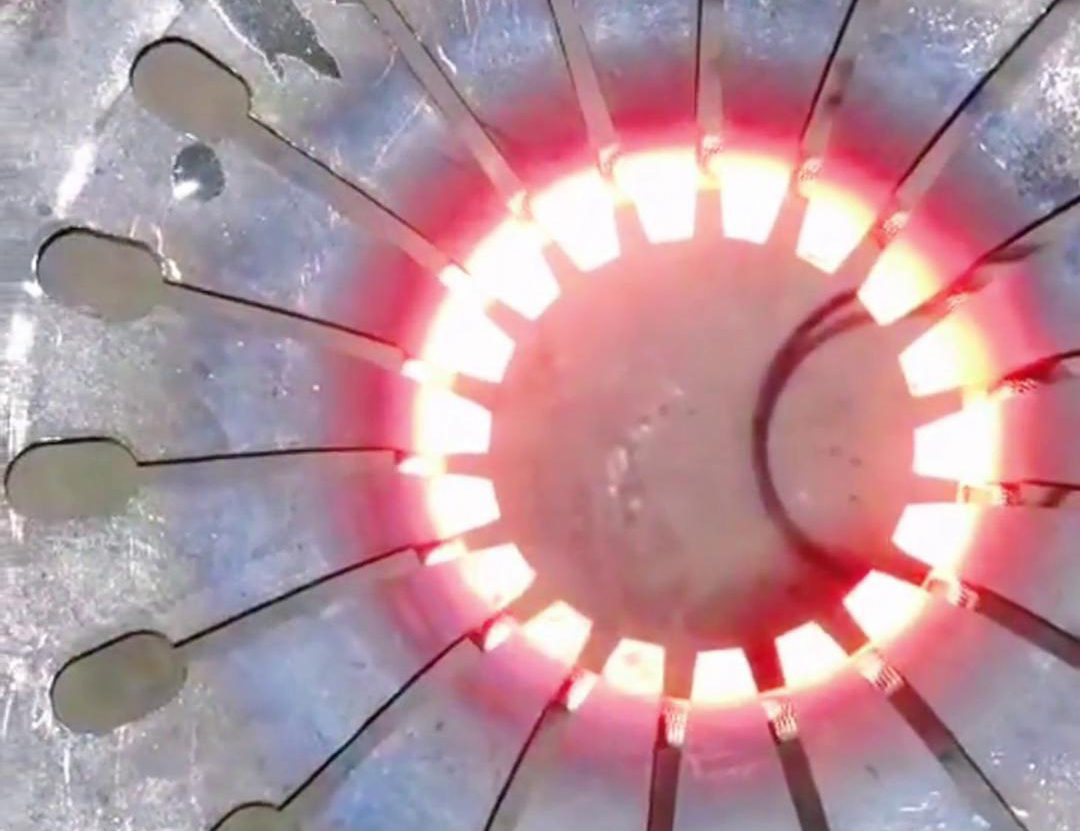
- 安全性冗余:汽车行驶中离合器失效可能引发安全事故,机床淬火的稳定质量为压盘提供性能冗余,避免人工操作误差导致的潜在风险;
- 工艺可控性:机床可记录每片压盘的淬火参数(温度、时间、冷却压力),实现全流程追溯,便于质量问题排查;
- 适配量产需求:全自动生产线单小时可处理 80-100 片压盘,效率是人工淬火的 5 倍,且能通过参数记忆快速切换不同型号压盘的淬火程序(换型时间≤10 分钟)。
尽管人工超高频淬火不适合汽车量产压盘,但在特定场景仍有价值:
- 压盘维修翻新(小批量处理,对一致性要求较低);
- 非车用压盘(如农机、工程机械离合器,工况相对缓和);
- 工艺调试阶段(快速测试不同淬火参数对压盘性能的影响)。
对汽车用离合器压盘而言,高频淬火机床通过 “全自动控制 + 精准参数匹配”,从根本上解决了人工淬火的质量波动问题,是保障离合器长期可靠运行的关键工艺选择。若需平衡成本与质量,可采用 “人工上料 + 机床自动淬火” 的半自动化方案,既保留操作灵活性,又确保核心淬火环节的稳定性。