不锈钢高频退火:消除应力、优化性能的精准工艺
作者:
小编
点击数:
发布日期: 2025-07-08
不锈钢在冷轧、冲压、焊接等加工过程中,会因晶格畸变产生内应力,不仅易导致后续加工或使用中出现变形、开裂,还可能破坏表面钝化膜,降低耐腐蚀性。高频退火技术通过对不锈钢的局部精准加热与缓冷,既能高效消除应力,又能改善表面状态与耐腐蚀性能,成为不锈钢精密加工中的关键工艺。
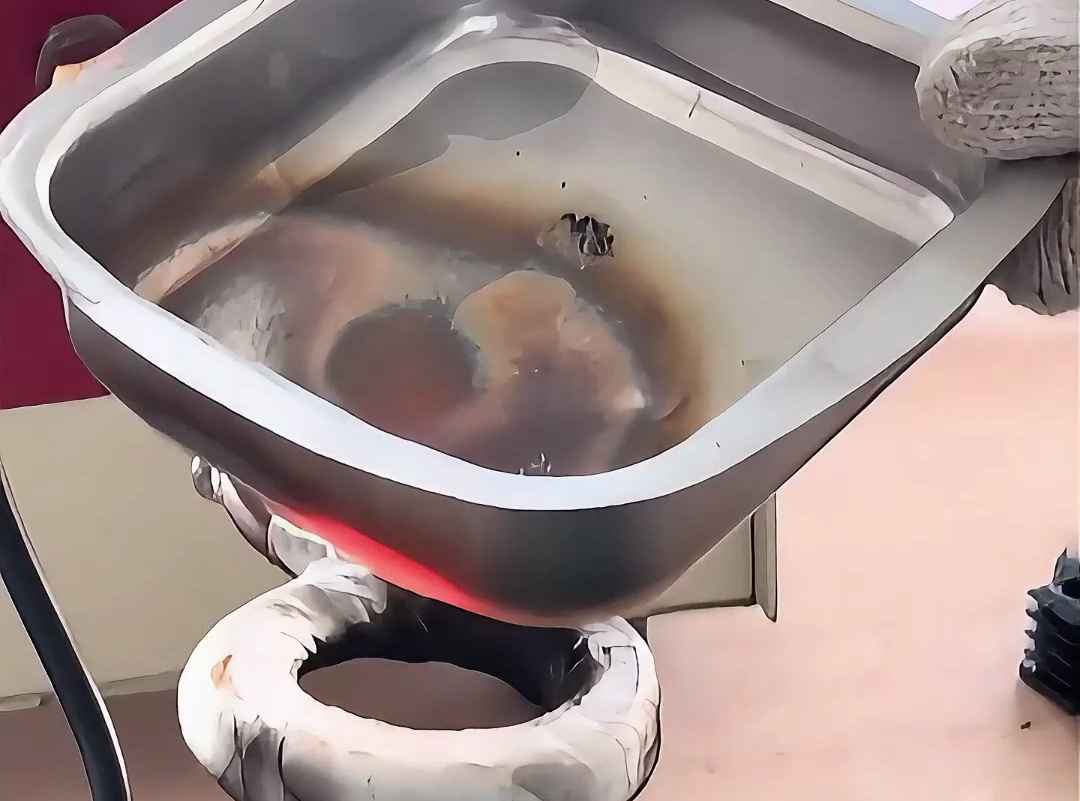
不锈钢(如 304、316、430 等)的加工应力主要源于:
- 冷轧时金属晶粒被强行拉长、压扁(产生 “冷作硬化”,硬度提升但脆性增加);
- 冲压折弯处的晶格错位(形成应力集中区,易在温差或外力下开裂);
- 焊接时局部高温导致的组织不均匀(产生焊接应力,可能引发晶间腐蚀)。
高频退火(频率通常 30-80kHz)通过以下过程消除应力:
- 精准加热:利用电磁感应使不锈钢工件自身发热,将应力集中区域加热至 “再结晶温度”(奥氏体不锈钢约 1050-1100℃,铁素体不锈钢约 750-850℃),此时被扭曲的晶粒重新形核、长大,恢复均匀组织;
- 缓慢冷却:达到目标温度后,控制冷却速度(通常≤5℃/ 秒),避免快速降温重新产生应力,使晶粒稳定排列,内应力可消除 80%-95%。
某精密机械厂数据显示:304 不锈钢薄板(厚度 1mm)经冷轧后,弯曲处应力达 300MPa,高频退火后应力降至 50MPa 以下,后续激光切割时开裂率从 25% 降至 0。
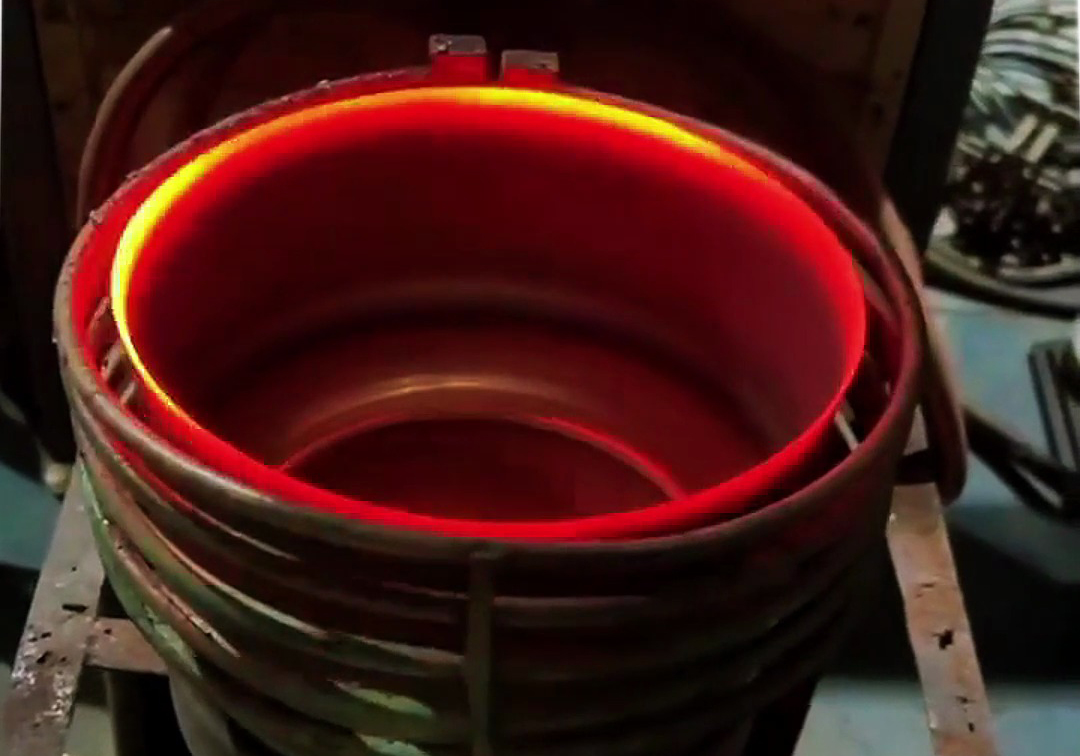
除消除应力外,高频退火还能针对性改善不锈钢的关键性能:
- 加工稳定性:消除应力后,不锈钢在后续铣削、钻孔等加工中,尺寸精度偏差可控制在 ±0.01mm(未退火件可能达 ±0.05mm);
- 使用可靠性:在温差变化大的环境(如厨房设备、化工管道)中,退火后的不锈钢因应力均衡,不会因热胀冷缩产生 “翘曲” 或 “微裂纹”。
- 冷轧或冲压导致的表面 “划痕、微凸”,在高频加热时会因金属轻微流动而 “抚平”,表面粗糙度(Ra)可从退火前的 1.6μm 降至 0.8μm 以下;
- 避免传统退火(如箱式炉)因长时间高温导致的 “氧化皮生成”,高频加热时间短(通常 10-30 秒),表面氧化层厚度≤3μm,无需酸洗即可保持不锈钢的原有光泽。
- 应力集中区域是不锈钢 “应力腐蚀开裂” 的敏感点,高频退火消除应力后,在盐雾环境中的耐腐蚀寿命延长 2-3 倍(如 316 不锈钢盐雾测试从 500 小时提升至 1500 小时);
- 均匀的组织使表面钝化膜(Cr₂O₃)分布更完整,减少因膜层破损导致的局部腐蚀(点蚀、缝隙腐蚀)。
不同类型不锈钢对高频退火的响应略有差异,但均能显著获益:
- 奥氏体不锈钢(304、316):消除冷轧应力,避免 “晶间腐蚀”(尤其焊接后的热影响区);
- 铁素体不锈钢(430):改善冲压后的脆性,提升折弯加工的合格率;
- 马氏体不锈钢(410):平衡硬度与韧性(退火后硬度降至 HRC20-25),适合刀具、阀门等需兼顾切削与耐蚀的部件。
典型应用场景包括:
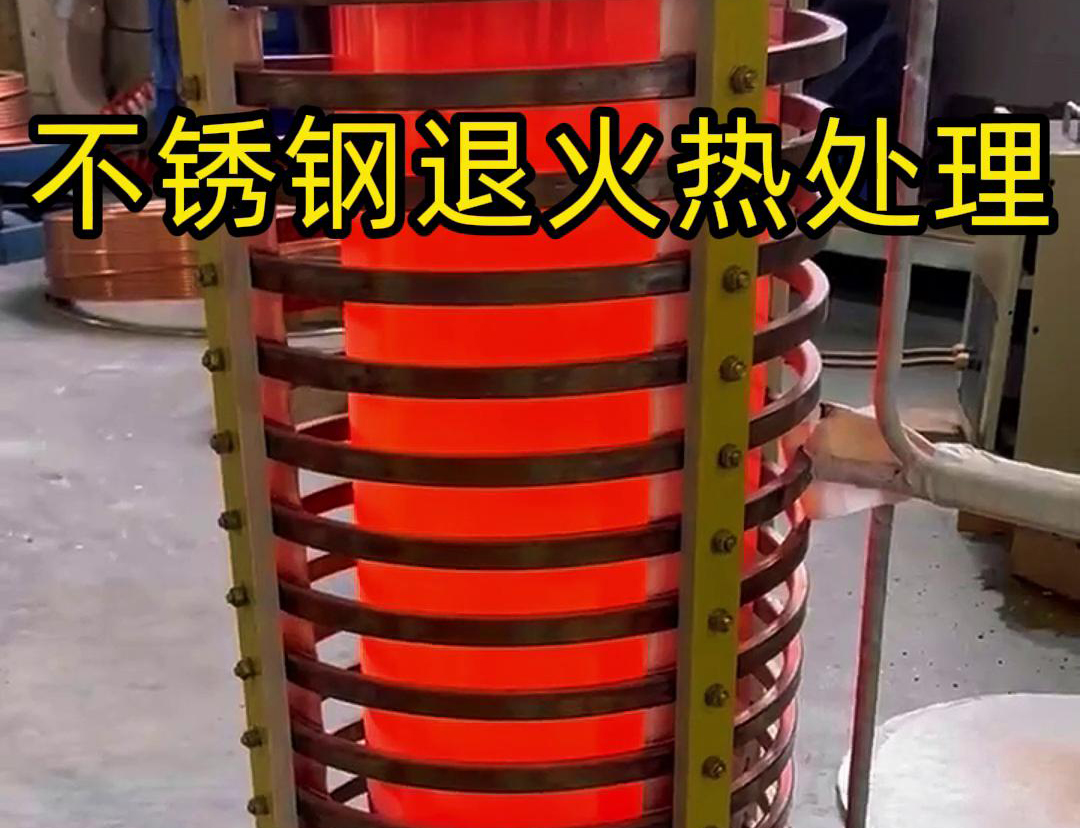
与传统退火工艺相比,高频退火在不锈钢处理中优势显著:
- 局部加热:仅针对应力集中区(如焊缝、折弯处)加热,不影响工件其他区域性能;
- 效率极高:单件处理时间是箱式炉退火的 1/20-1/50(如 304 不锈钢管件退火仅需 15 秒);
- 节能环保:能耗仅为传统退火的 30%-50%,且无燃料燃烧废气排放。
高频退火通过对不锈钢微观组织的精准调控,从根源上解决了加工应力带来的系列问题,既保证了尺寸稳定性,又提升了表面质量与耐腐蚀性,尤其适合对精度、外观、寿命有高要求的不锈钢制品。对于不锈钢加工企业而言,这一工艺不仅能降低废品率,更能提升产品的市场竞争力 —— 毕竟 “无应力、高耐蚀” 的不锈钢,才是真正 “好用” 的不锈钢。