高频加热机在铝板退火中的应用:优化铝板性能的关键技术
作者:
小编
点击数:
发布日期: 2025-02-14
在铝板加工过程中,残余应力和过硬化现象往往会影响铝板的质量与后续加工。铝板退火工艺则是解决这些问题的重要手段,其主要目的在于消除残余应力、改善过硬化状况,以此提升材料的韧性与可加工性。高频加热机凭借其高效、精准的加热特性,通过将铝板加热到 200 度并进行相应的保温与冷却处理,促使铝板内部微观结构改变,实现退火目的,在铝板加工领域发挥着关键作用。
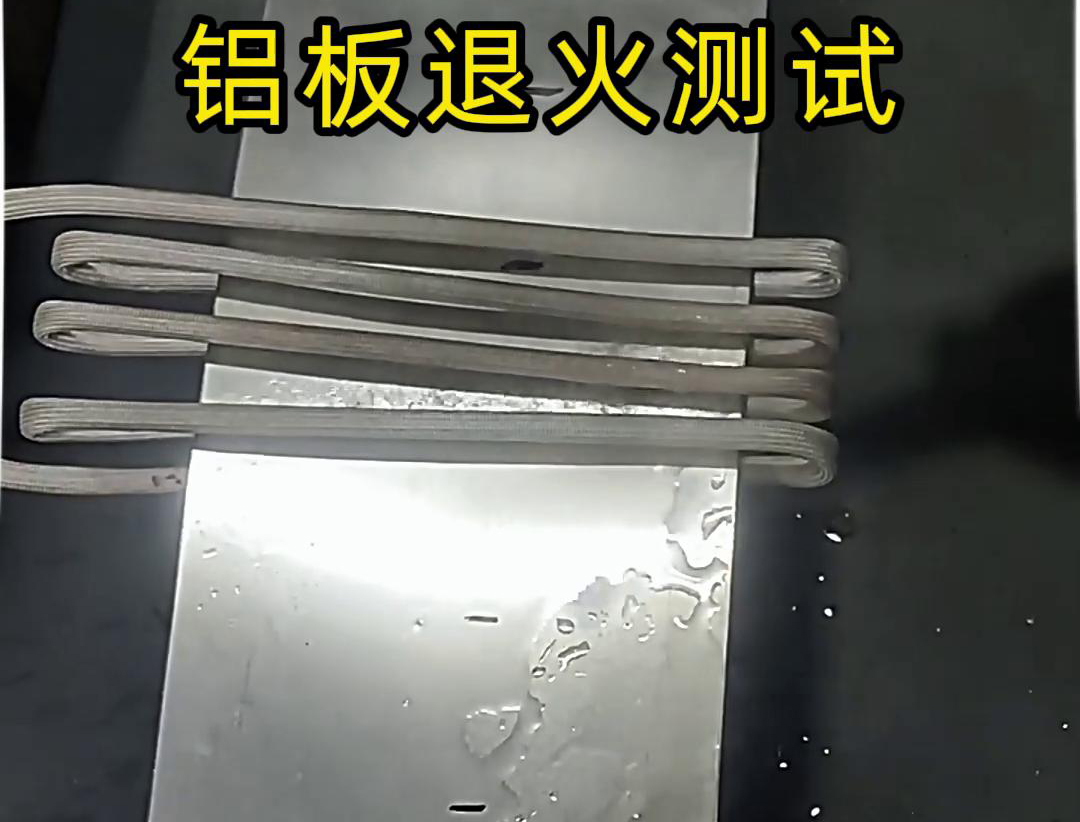
在铝板的轧制、切割等加工过程中,不可避免地会产生残余应力。这些残余应力会导致铝板在后续使用中出现变形、开裂等问题,严重影响产品质量。例如,在建筑幕墙铝板的安装后,残余应力可能使铝板逐渐变形,影响幕墙的平整度和美观度。通过退火,铝板内部的原子获得足够能量进行重新排列,从而有效消除残余应力,提高铝板尺寸稳定性,延长其使用寿命。
铝板在冷加工过程中,位错大量增殖且相互缠结,导致材料硬度增加、塑性降低,即出现过硬化现象。这使得铝板在后续加工,如弯曲、冲压等过程中,容易发生破裂。退火能够使铝板内部的位错重新分布,降低位错密度,从而改善过硬化现象,恢复材料的塑性,提高其可加工性。例如,在汽车制造中,经过退火处理的铝板更易于冲压成各种复杂形状的车身部件。
残余应力和过硬化现象的改善,直接提升了铝板的韧性。韧性良好的铝板在受到冲击载荷时,能够吸收更多能量而不发生脆性断裂。这在航空航天领域尤为重要,如飞机的机翼、机身等部位使用的铝板,需具备高韧性以应对飞行过程中的各种复杂受力情况。
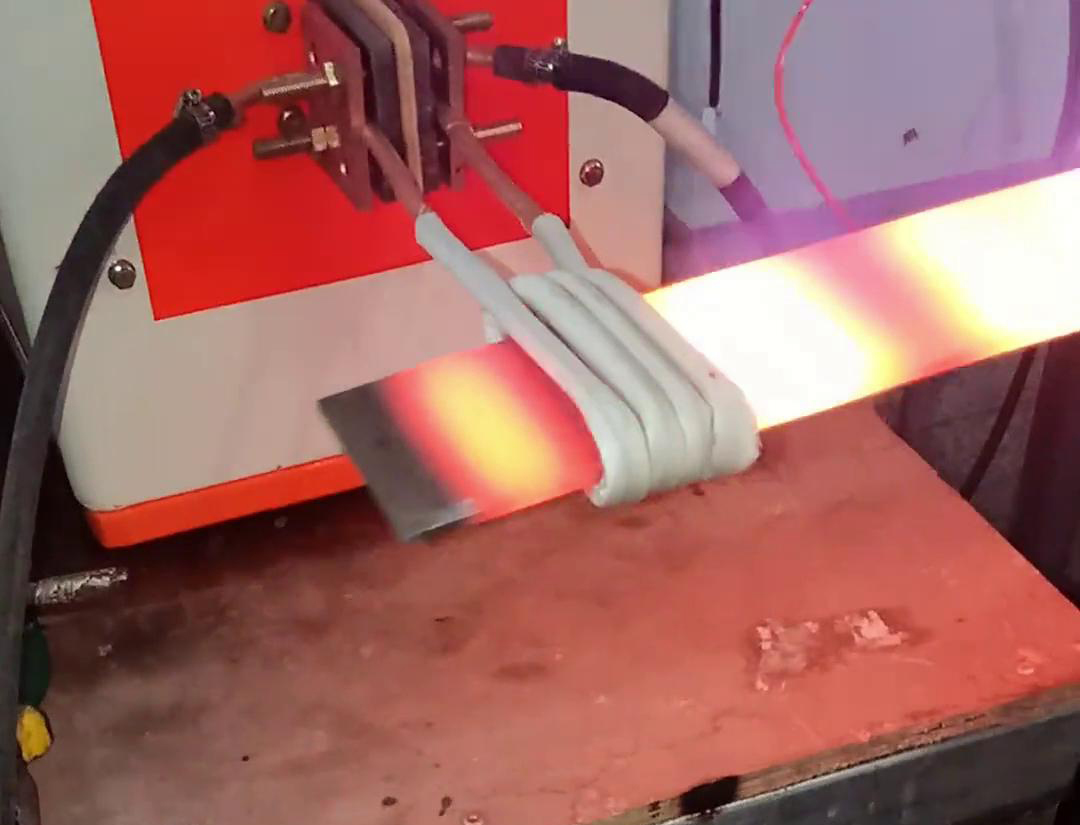
高频加热机基于电磁感应原理工作。当高频电流通过感应线圈时,产生高频交变磁场。铝板置于该磁场中,内部产生感应电流(涡流),由于铝板本身具有电阻,根据焦耳定律,电能迅速转化为热能,使铝板快速升温至 200 度。在达到目标温度后,通过精确控制加热功率,保持该温度一段时间进行保温,使铝板内部微观结构充分调整。之后,进行冷却处理,完成退火过程。
- 快速加热:高频加热机能够在短时间内将铝板加热到 200 度,相比传统加热方式,如电阻炉加热,可大大缩短加热时间,提高生产效率。例如,传统加热方式可能需要数十分钟才能使铝板达到目标温度,而高频加热机仅需几分钟,有效减少了生产周期。
- 精准控温:配备高精度的温度控制系统,高频加热机能够精确设定和控制加热温度、保温时间以及冷却速度。在铝板退火过程中,温度控制精度可达 ±5℃,确保铝板在合适的温度范围内进行退火,保证了退火质量的稳定性和一致性。
- 节能高效:高频加热机直接在铝板内部产生热量,热量散失少,能量利用率高。与传统加热方式相比,可有效降低能源消耗,符合现代制造业节能环保的发展趋势。
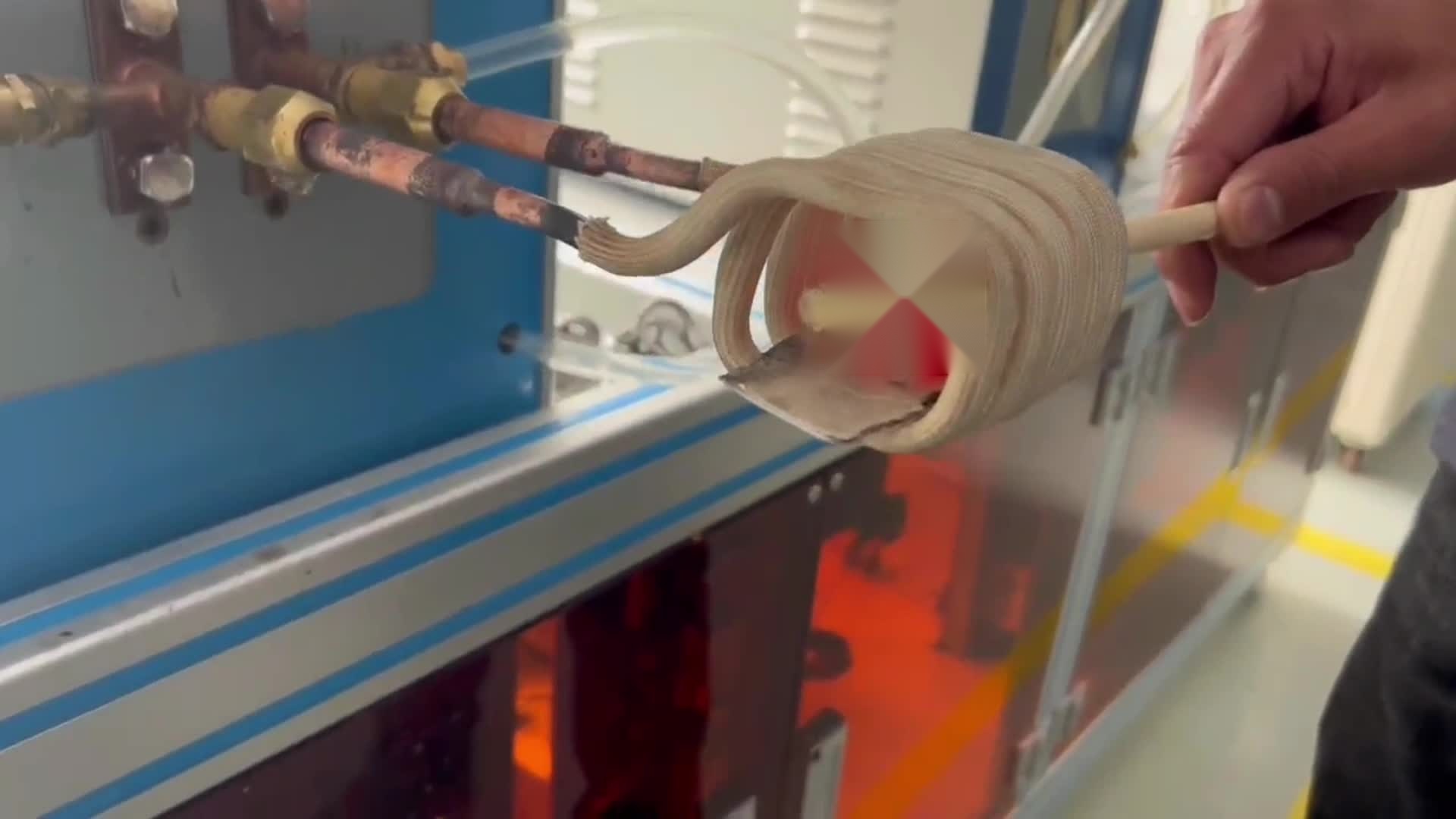
- 功率选择:根据铝板的厚度、尺寸以及加热速度要求,合理选择高频加热机的功率。一般来说,对于较厚的铝板,需要选择较高功率以保证快速升温;而对于较薄的铝板,适当降低功率可避免局部过热。
- 升温速率:控制合适的升温速率至关重要。过快的升温速率可能导致铝板内部热应力过大,引起变形甚至开裂;过慢的升温速率则会降低生产效率。通常,升温速率可控制在每分钟 10 - 30 度之间,具体数值需根据铝板实际情况调整。
- 保温时间:保温时间取决于铝板的材质、厚度以及加热设备的特性。保温时间过短,铝板内部微观结构无法充分调整,影响退火效果;保温时间过长,则会增加生产成本且可能导致铝板晶粒长大,降低材料性能。一般情况下,保温时间在 10 - 30 分钟之间。
- 温度均匀性:在保温阶段,确保铝板各部位温度均匀非常关键。通过优化感应线圈的设计和磁场分布,以及采用适当的搅拌或循环装置,可使铝板在保温过程中温度均匀,保证退火质量。
- 冷却方式:冷却方式对铝板的最终性能有重要影响。常见的冷却方式有水冷、风冷和自然冷却等。对于一些对韧性要求较高的铝板,可采用风冷或自然冷却,以获得较好的韧性;而对于一些对硬度要求较高的铝板,可适当加快冷却速度,如采用水冷,但需注意控制冷却速度,防止产生过大的内应力。
- 冷却速度:合理控制冷却速度能有效调整铝板的微观结构和性能。过快的冷却速度可能导致残余应力再次产生,而过慢的冷却速度则可能影响生产效率。通常,冷却速度可根据铝板的材质和性能要求进行调整,一般在每分钟 5 - 20 度之间。
高频加热机在铝板退火中具有显著优势,通过精确控制加热、保温和冷却过程,能够有效消除铝板残余应力和过硬化现象,提高其韧性和可加工性。随着铝板在各个领域应用的不断拓展,高频加热机退火工艺有望得到进一步优化和广泛应用,推动铝板加工行业的技术进步与发展。