轴类淬火选择数控高频淬火机床确实具有诸多显著优势
作者:
小编
点击数:
发布日期: 2025-02-17
轴类淬火选择数控高频淬火机床确实具有诸多显著优势,以下是对这些优势的详细分析:
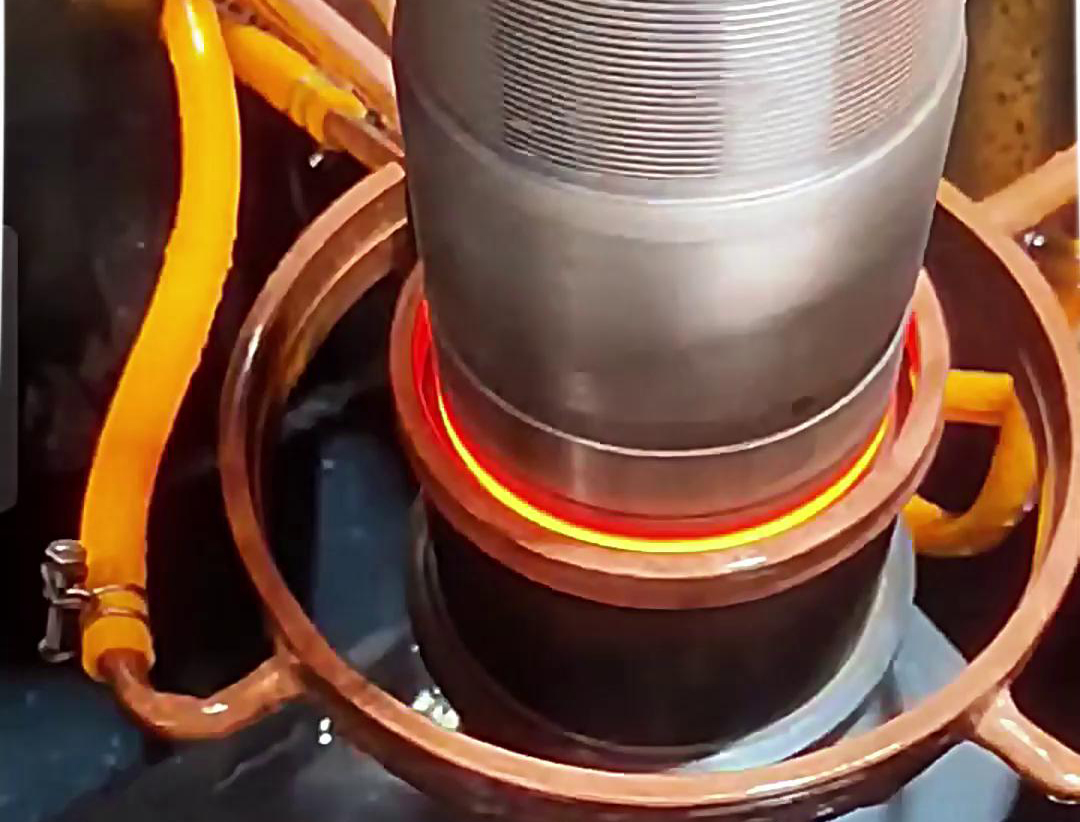
- 精准控制
- 温度精准:数控高频淬火机床配备了先进的温度控制系统,能够精确地控制加热温度。通过高精度的温度传感器实时监测工件的温度,并将数据反馈给控制系统,控制系统根据预设的温度值自动调整加热功率,确保轴类工件在淬火过程中达到并保持精确的淬火温度,从而保证淬火质量的稳定性和一致性。
- 加热区域精准:可以通过精确控制高频感应线圈的形状、尺寸和位置,以及调整感应电流的分布,实现对轴类工件特定部位的精准加热。例如,对于一些需要局部淬火的轴类零件,能够准确地将加热区域限制在需要淬火的部位,避免了不必要的加热和淬火,提高了工件的性能和质量。
- 高效加热
- 快速升温:利用高频电磁场的集肤效应和邻近效应,使轴类工件表面迅速产生感应电流,从而实现快速加热。与传统的加热方式相比,数控高频淬火机床的加热速度要快得多,可以在短时间内将轴类工件加热到淬火所需的温度,大大提高了生产效率。
- 批量处理:能够实现连续或批量生产,通过自动化的上下料装置和生产线集成,可对多个轴类工件进行连续淬火处理,减少了生产过程中的等待时间,提高了生产效率和产能。
- 自动化操作
- 减少人力成本:数控系统可以根据预设的程序自动完成淬火过程的各个环节,包括工件的上下料、加热、冷却等操作,大大减少了人工操作的工作量和劳动强度,降低了对操作人员技能水平的依赖,同时也减少了人为因素对淬火质量的影响。
- 提高生产稳定性:自动化操作能够保证每个工件的淬火过程都按照相同的程序和参数进行,避免了人工操作可能出现的误差和不一致性,提高了生产过程的稳定性和可靠性,有利于保证产品质量的一致性。
- 适应性强
- 多种轴类适配:可以通过调整设备的参数和更换不同的感应线圈,适应不同尺寸、形状和材料的轴类工件的淬火需求。无论是细长轴、短粗轴,还是具有复杂形状的轴类零件,都能够通过合理的工艺调整和设备配置实现高效的淬火处理。
- 工艺参数可调:数控系统允许操作人员根据不同的工件材料、尺寸和淬火要求,灵活调整加热时间、加热功率、冷却方式和冷却时间等工艺参数,以实现最佳的淬火效果。这种灵活性使得数控高频淬火机床能够满足各种不同的生产需求,适应多样化的市场需求。
- 质量稳定
- 组织性能均匀:由于精准的温度控制和均匀的加热方式,能够使轴类工件表面获得均匀的组织和性能。在淬火过程中,工件表面的硬度、强度和韧性等性能指标更加稳定和一致,减少了因组织不均匀导致的工件变形、开裂等质量问题,提高了产品的合格率和使用寿命。
- 质量可追溯:数控系统可以记录每个工件的淬火工艺参数和生产数据,如加热温度、加热时间、冷却时间等,为产品质量追溯提供了有力的依据。一旦出现质量问题,可以通过查阅生产记录,快速分析原因,采取相应的改进措施,有助于提高产品质量的管理水平。
- 节能环保
- 能源利用率高:高频淬火是一种直接加热方式,热量主要集中在工件表面,热量散失少,能源利用率高。与传统的加热方式相比,数控高频淬火机床能够在相同的生产条件下,消耗更少的能源,降低了生产成本,同时也符合现代制造业对节能环保的要求。
- 减少环境污染:由于加热速度快,工件在高温下停留的时间短,减少了氧化和脱碳现象的发生,降低了对环境的污染。同时,数控高频淬火机床采用的冷却介质通常是水或水溶性淬火剂,相对传统的油淬火等方式,更加环保,减少了废弃物的产生和处理成本。
- 数据记录与分析
- 生产过程监控:数控高频淬火机床的控制系统可以实时记录生产过程中的各种数据,如温度、功率、时间等参数,操作人员可以通过监控界面随时查看生产状态和数据,及时发现生产过程中的异常情况,便于进行调整和优化。
- 工艺优化依据:通过对大量生产数据的分析,可以深入了解淬火工艺对工件质量的影响规律,为工艺优化提供有力的依据。根据数据分析结果,可以调整工艺参数,改进生产工艺,提高淬火质量和生产效率,实现生产过程的持续改进。