高频加热机与机械手臂协同:金属加工自动化新方案
作者:
小编
点击数:
发布日期: 2025-02-25
在现代工业生产中,高频加热机与机械手臂的协同应用,正推动金属加工行业向高效化、智能化方向发展。这种组合解决方案可实现金属工件加热、淬火、焊接等工艺的全流程自动化,适用于汽车制造、航空航天、电子元件等多领域需求。
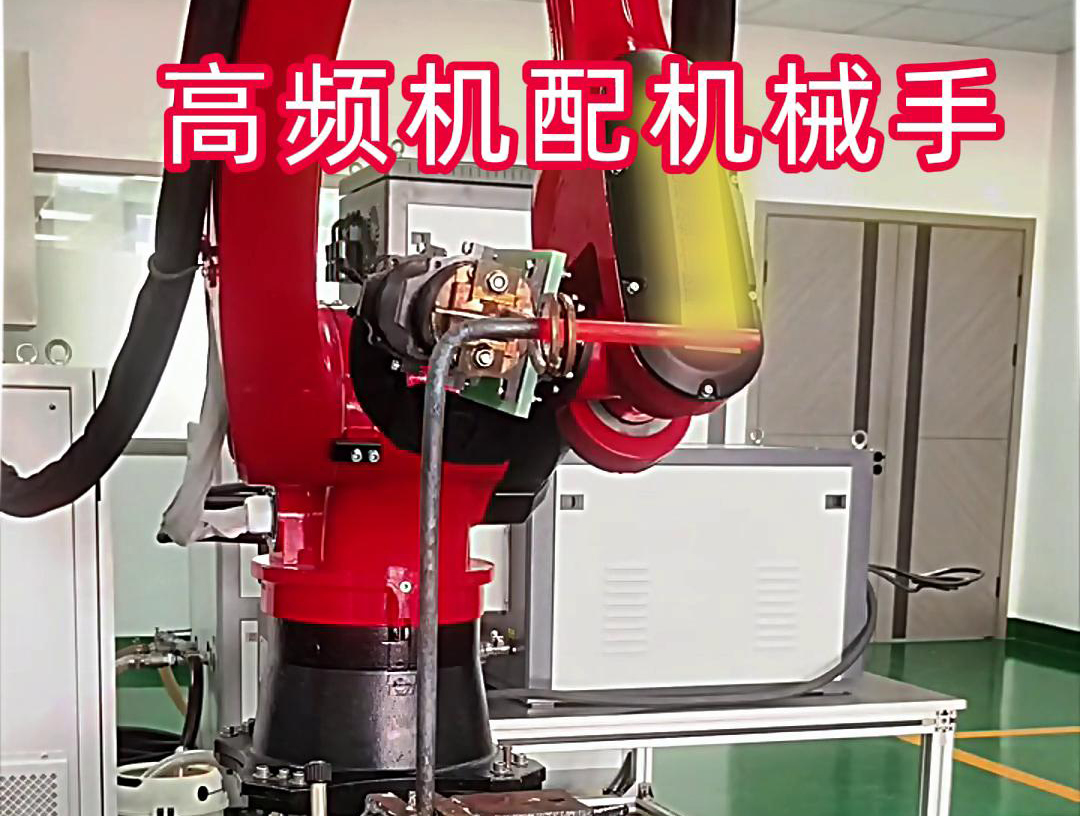
该系统由高频加热机与可编程机械手臂组成:
- 高频加热设备:支持功率 0-100kW 调节,频率范围 20-400kHz,可适配不同金属材质(钢、铝、铜等)的加热需求。
- 六轴机械手臂:定位精度 ±0.05mm,负载能力 5-50kg,支持轨迹编程和视觉引导。
- 控制系统:通过 PLC 或工业 PC 实现加热参数与机械动作的同步控制,支持实时数据采集与追溯。
- 工件上料:机械手臂通过吸盘或夹爪从料仓抓取待加工工件。
- 加热处理:
- 淬火:将工件移送至高频感应线圈内,按预设参数(如功率 80kW、时间 3 秒)完成表面加热后,由集成喷头喷水淬火。
- 焊接:机械手臂带动加热头对焊缝进行局部加热,配合送丝机构完成钎焊或熔焊。
- 质量检测:集成红外测温或激光扫描装置,实时检测加热温度和工件变形量。
- 下料分拣:合格品移送至成品区,不良品自动剔除。
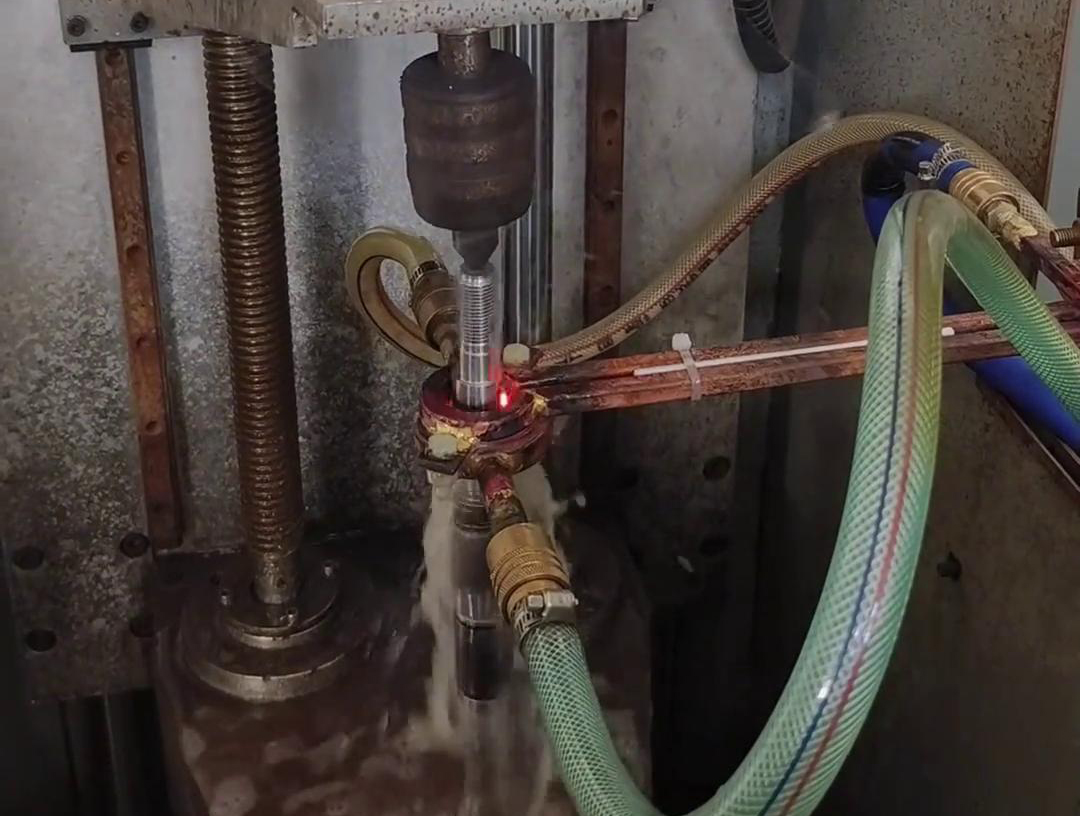
- 柔性生产能力:
- 支持多品种工件混线生产,通过更换感应线圈和调整程序即可切换工艺。
- 典型换型时间:3-10 分钟(取决于工件复杂度)。
- 工艺一致性提升:
- 加热温度控制精度 ±3℃,相比人工操作波动减少 70%。
- 机械重复定位精度保障工件处理位置偏差 < 0.1mm。
- 生产效率优化:
- 以汽车连杆淬火为例,单台设备产能可达 1200 件 / 小时,较传统人工线提升 3 倍。
- 能源利用率达 85% 以上,较火焰加热节能 40%。
- 安全环保特性:
- 全封闭作业减少辐射泄漏,符合 ISO 13485 安全标准。
- 淬火介质循环利用率 90%,废烟废气排放量低于国家标准限值。
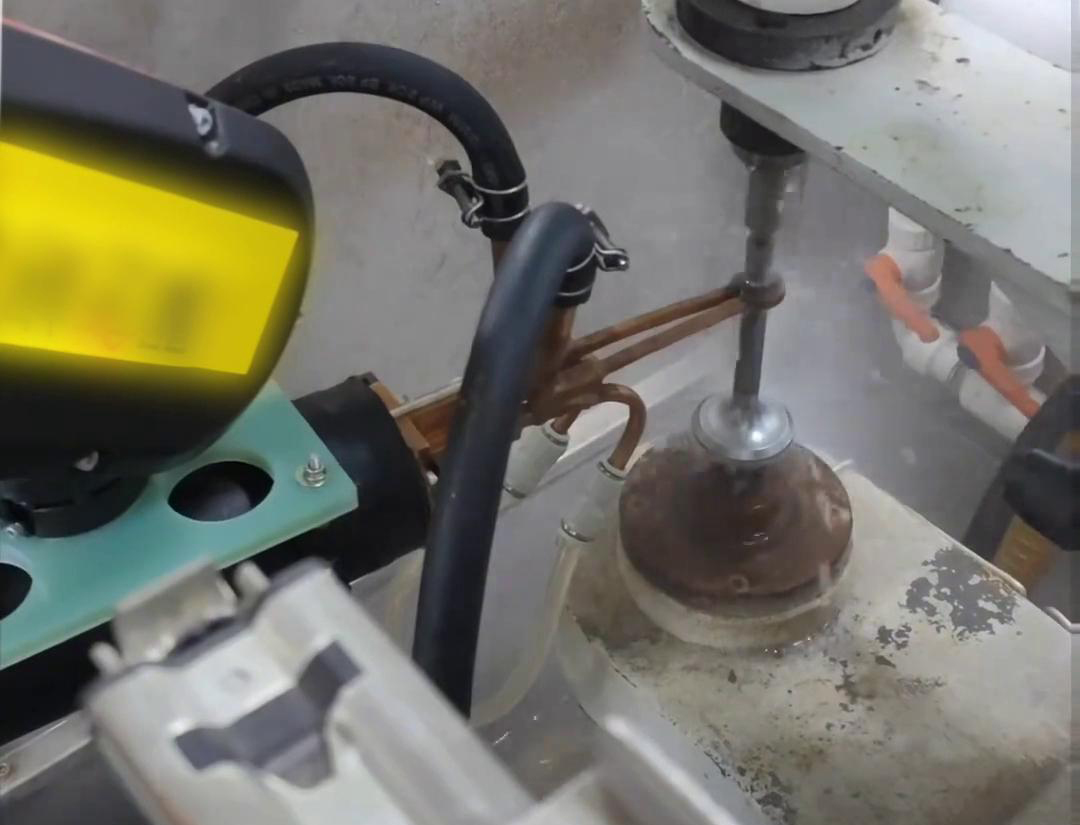
- 汽车零部件:用于 CVT 变速箱齿轮淬火,硬化层深度 0.8-1.2mm,表面硬度 HRC55±2。
- 航空航天:钛合金叶片榫头局部强化,加热时间精确至 0.5 秒,避免基体组织过热。
- 电子制造:5G 基站散热器铜管焊接,实现无氧化焊接,焊缝抗拉强度≥母材 85%。
高频加热机与机械手臂的自动化组合,为金属加工行业提供了高效、稳定且环保的解决方案。随着工业 4.0 技术的深入应用,该系统可进一步集成 AI 算法,实现工艺参数的自适应优化和预测性维护,助力制造业向智能化转型升级。