高频自动化钎焊设备:制冷配件焊接的智能化升级
作者:
小编
点击数:
发布日期: 2025-02-25
在空调制冷行业,铜件、铝件及各类管件接头的焊接质量直接影响产品性能。高频自动化钎焊设备通过电磁感应加热技术与自动化控制的结合,为行业提供了高效、稳定的焊接解决方案,推动生产模式向智能化转型。
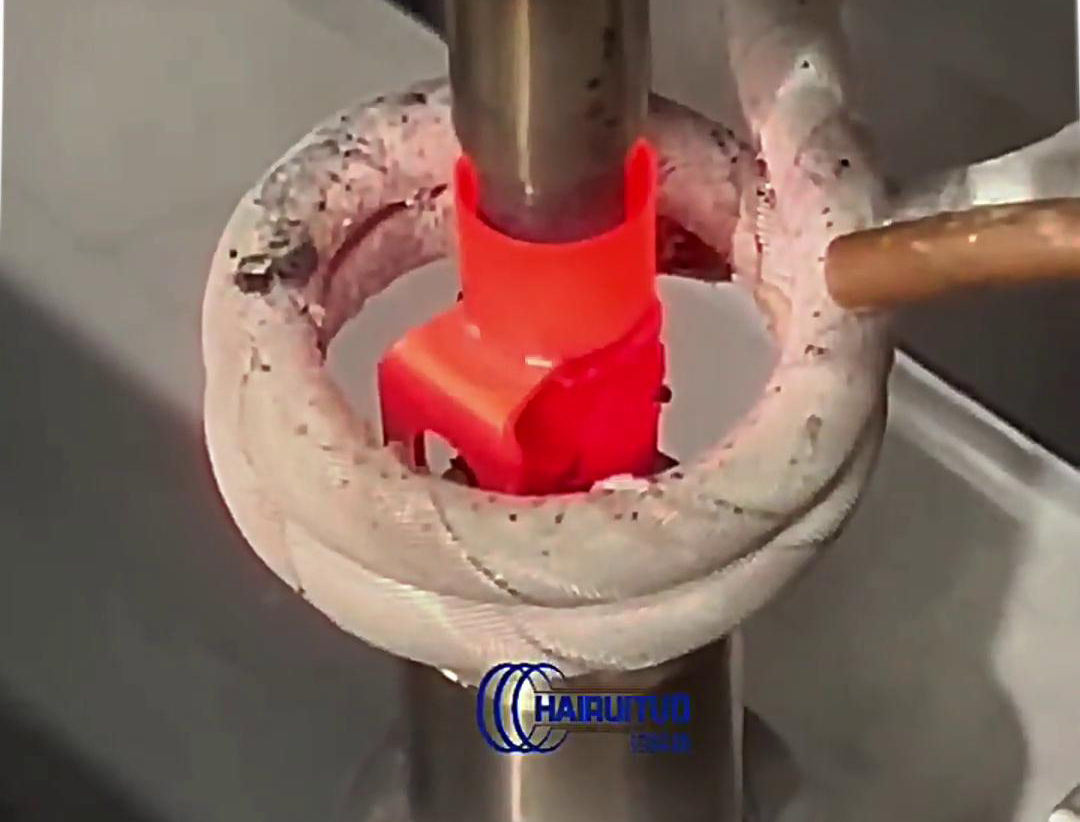
传统手工火焰钎焊存在显著局限性:
- 效率瓶颈:单工位焊接耗时约 30-60 秒,难以满足规模化生产需求
- 质量波动:依赖焊工经验,焊缝合格率约 85-90%
- 成本压力:熟练焊工培养周期长,人力成本占比达 25-30%
高频自动化钎焊设备通过以下技术突破解决行业难题:
- 非接触式加热:利用电磁感应原理,5 秒内达到钎焊温度(铜件约 600-700℃)
- 精准控温:温度偏差 ±5℃,确保钎料均匀润湿
模块化设计:支持铜 - 铜、铜 - 铝、铝 - 铝等多种材料组合焊接
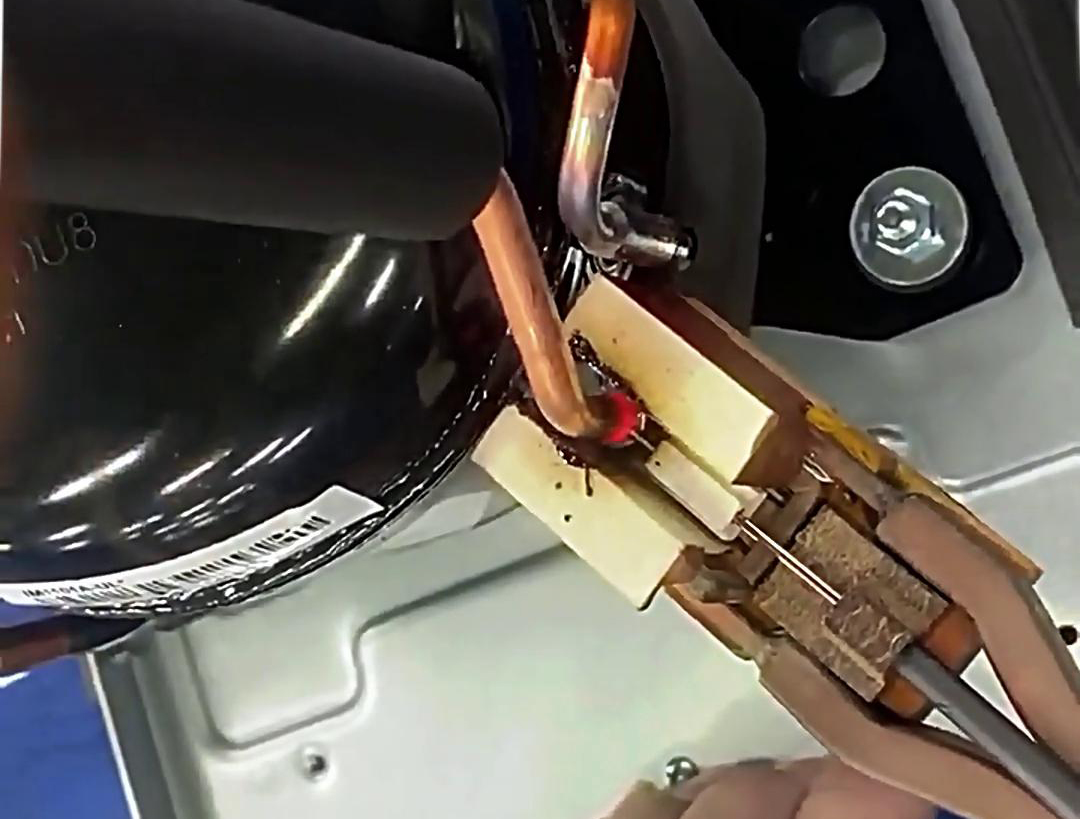
- 人工上料→机械臂夹持工件→高频加热→自动送丝焊接→卸料检测
- 适用于多规格管件小批量生产,单工位产能提升至 15-20 件 / 分钟
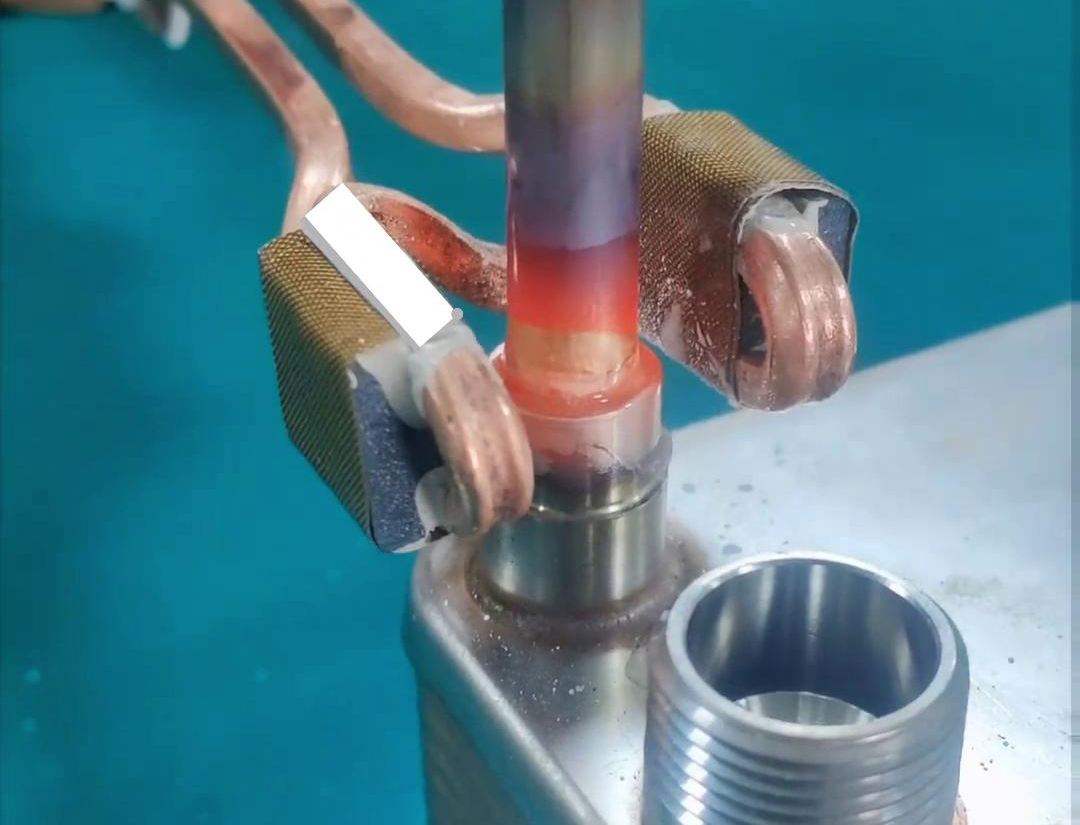
- 工艺适应性:
- 支持 Φ6-Φ50mm 管径,壁厚 0.5-3mm 的管件焊接
- 可调节参数:功率(0-100kW)、频率(20-400kHz)、加热时间(0.1-10 秒)
- 成本优化:
- 单台设备可替代 3-5 名焊工,综合成本降低 40-60%
- 电能利用率 85%,较燃气加热节能 35%
- 质量稳定性:
- 焊缝抗拉强度≥母材 80%(铜件≥200MPa)
- 气密性检测泄漏率 < 1×10⁻⁹Pa・m³/s
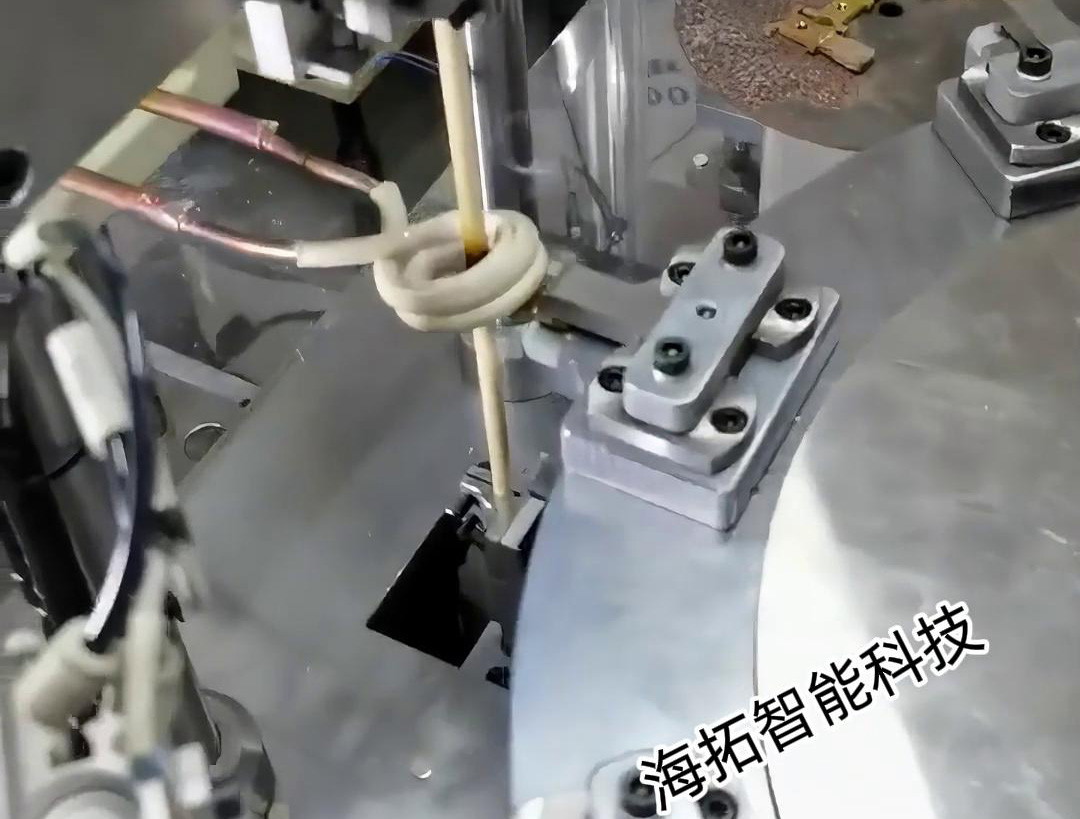
- 空调部件:
- 制冷设备:
- 新能源领域:
某制冷配件厂商采用自动化钎焊线后:
- 日产能从 8000 件提升至 25000 件
- 产品不良率从 7% 降至 1.2%
- 单班人力需求从 12 人减少至 3 人
高频自动化钎焊设备通过技术创新,实现了制冷配件焊接的高效化、智能化。随着工业机器人技术的发展,该系统可进一步集成 AI 视觉检测、自适应参数调整等功能,为行业高质量发展提供持续动力。