高频淬火:齿轮性能与成本的精准平衡术
作者:
小编
点击数:
发布日期: 2025-07-11
在齿轮制造中,高频淬火以 “局部强化 + 性能梯度” 设计,完美解决了 “表面耐磨” 与 “芯部抗冲击” 的矛盾,同时以高效、低成本特性成为中碳钢齿轮的首选表面强化工艺,其对性能与成本的平衡逻辑值得深入解析。
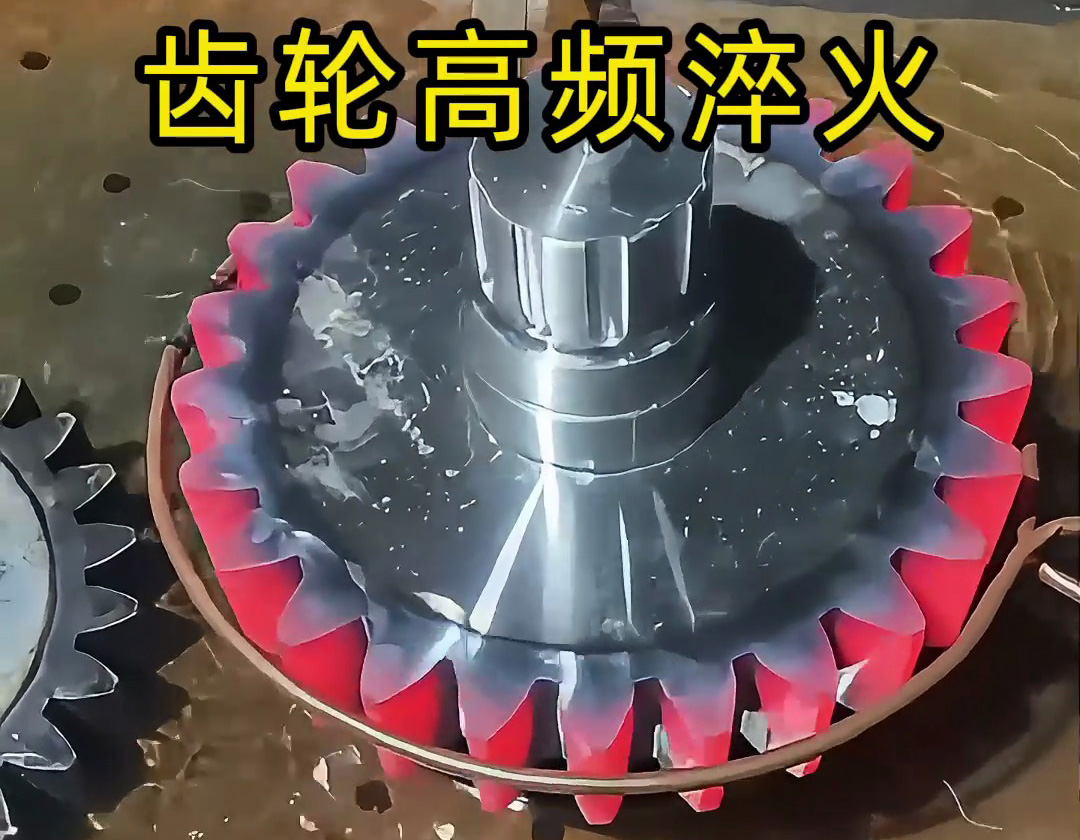
齿轮在啮合传动中,齿面承受接触应力(易磨损、疲劳点蚀),齿根承受弯曲应力(易断裂),高频淬火通过 “选择性硬化” 实现性能分化:
- 齿面高硬度抗磨损:高频感应加热使齿面(包括齿顶、齿侧、齿根过渡区)快速升温至 850-900℃,淬火后硬度达 HRC55-62,形成耐磨 “硬壳”,接触疲劳寿命提升 2-3 倍(对比未淬火齿轮);
- 齿芯高韧性抗冲击:仅齿面 3-5mm 深度硬化,齿芯仍保持原始韧性组织(HRC30-35),可吸收冲击载荷(如启动、制动时的瞬时过载),避免整体淬火导致的脆性断裂。
这种 “硬面韧芯” 结构,使齿轮在重载、高频啮合工况下(如汽车变速箱、工程机械减速器)既能抵抗磨损,又能承受冲击,综合性能远超整体调质处理。
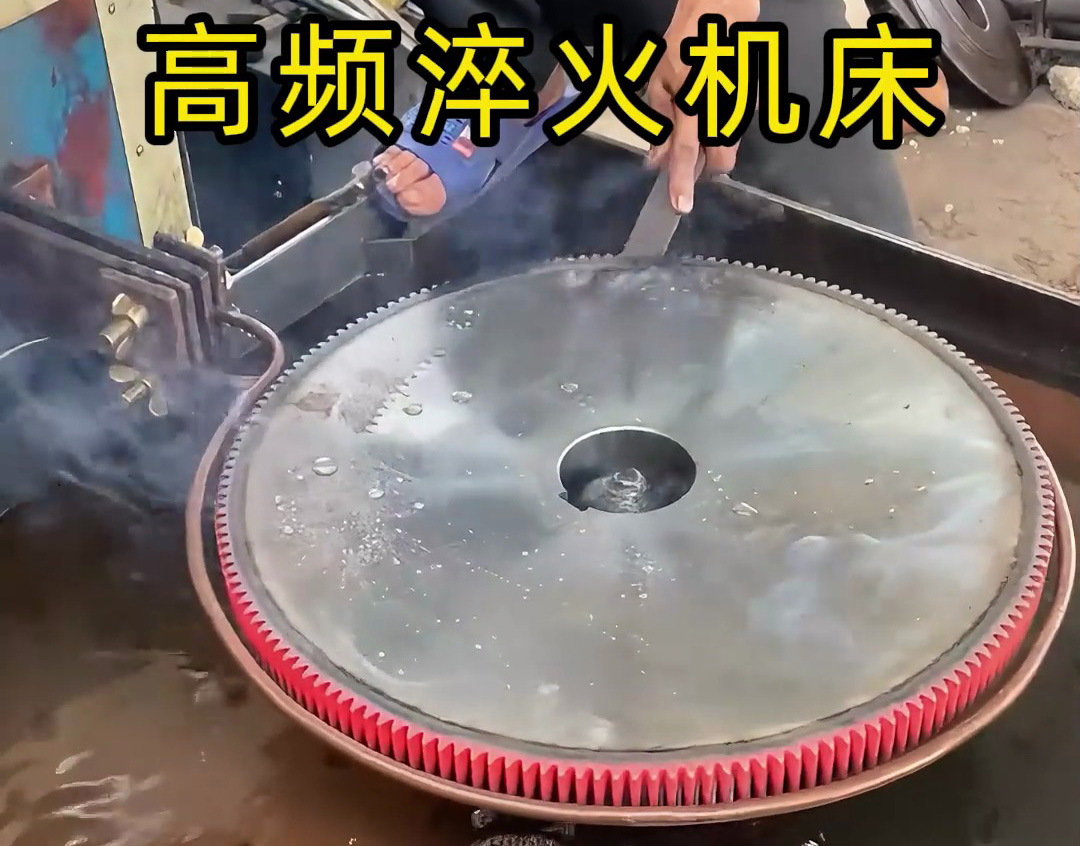
高频淬火相较渗碳、氮化等表面强化工艺,在成本控制上优势显著:
工艺对比项 | 高频淬火 | 渗碳淬火 | 气体氮化 |
---|
加工周期 | 单齿加热仅需 5-10 秒,批量处理效率高 | 需 20-40 小时(渗碳 + 淬火 + 回火) | 需 10-30 小时(氮化保温) |
设备投入 | 高频机 + 简单工装,成本约 10-30 万元 | 渗碳炉 + 淬火槽,成本约 50-200 万元 | 氮化炉系统,成本约 30-100 万元 |
材料要求 | 适配中碳钢(如 45# 钢、40Cr),无需高合金 | 需低碳合金结构钢(如 20CrMnTi) | 需含 Cr、Al 等合金元素的专用钢 |
后续加工 | 变形量≤0.05mm/m,无需复杂校直 | 变形大(≥0.1mm/m),需多道磨削 | 变形小但硬化层浅(≤0.3mm) |
以年产 10 万件中碳钢齿轮为例,高频淬火的综合成本(设备折旧 + 能耗 + 人工)仅为渗碳工艺的 50%-60%,且因材料门槛低(可用廉价中碳钢),原材料成本再降 10%-15%。
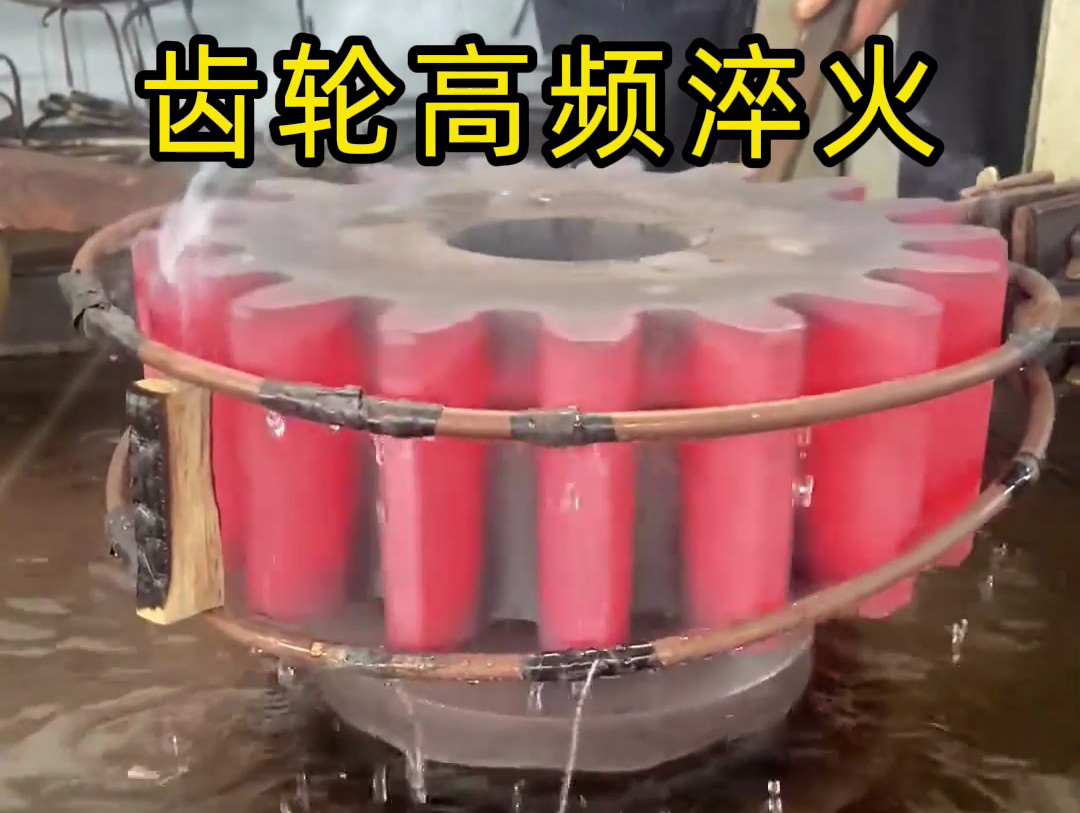
中碳钢(如 45# 钢)含碳量适中(0.42%-0.50%),经高频淬火后:
- 齿面可形成均匀马氏体组织(硬度达标),无需额外添加合金元素;
- 芯部保持珠光体 + 铁素体组织(韧性充足),无需复杂合金化设计。
这种材料与工艺的 “天然适配”,使中碳钢齿轮经高频淬火后,性能可满足多数工业传动需求(如载货汽车后桥齿轮、机床变速箱齿轮),而成本仅为合金齿轮的 60%-70%。
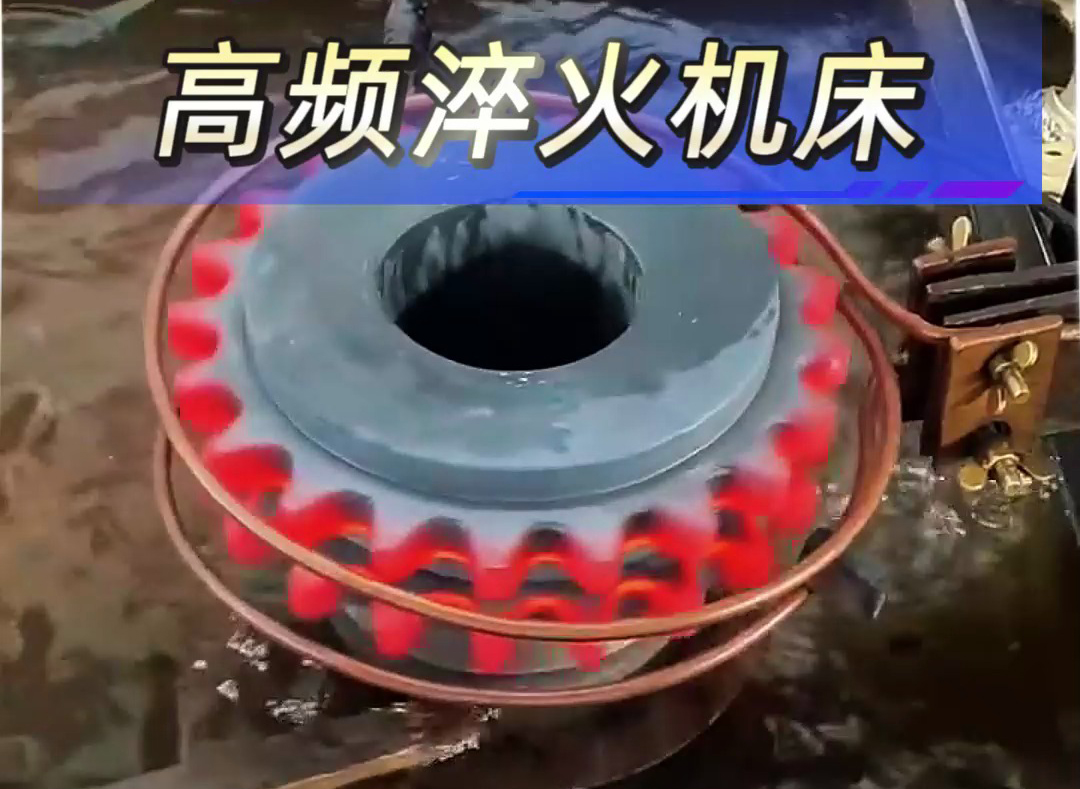
高频淬火对齿轮的提升,本质是 “用最少的资源实现最关键的强化”:
- 性能上:聚焦齿面与齿根(失效高发区)强化,不浪费能量硬化非受力区域;
- 成本上:省去渗碳的长时间保温、氮化的专用设备,以 “快速局部加热” 压缩时间与能耗;
- 质量上:变形量小(热影响区≤2mm),后续加工余量减少 30%,进一步降低制造成本。
对于中碳钢齿轮,高频淬火不是 “退而求其次” 的选择,而是 “性能达标 + 成本可控” 的最优解。它用精准的局部强化,让齿轮在 “耐磨 - 抗冲击” 性能上不妥协,同时以高效工艺将成本控制在合理范围,成为平衡齿轮性能与制造成本的 “核心工艺”。