销子全自动淬火设备:无人化生产的效率与质量革命
作者:
小编
点击数:
发布日期: 2025-07-10
销子(广泛用于机械定位、传动连接)的淬火质量直接影响其耐磨性与抗剪切强度,全自动高频淬火设备通过 “振动盘自动上料 + 机械夹具精准操作 + PLC 程序全程控温” 的模式,实现从进料到淬火完成的无人化生产,彻底消除人工操作的质量波动,成为批量销子生产的 “效率利器”。
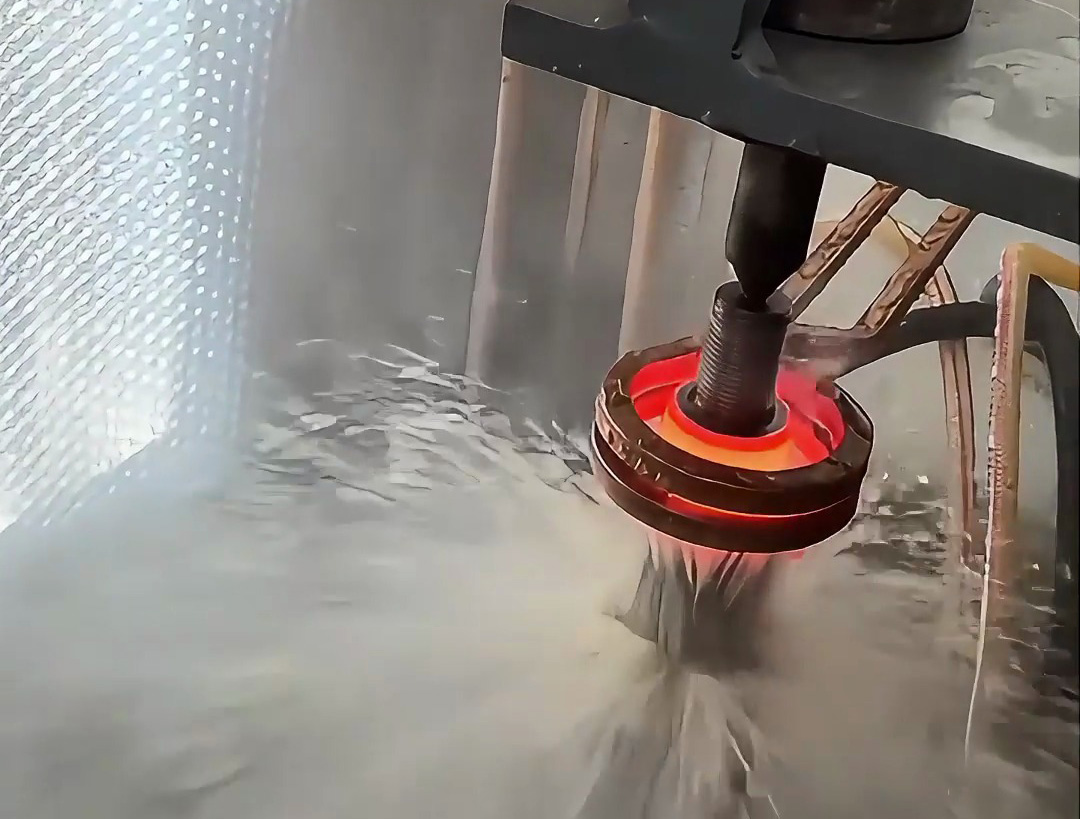
这套设备将高频淬火技术与自动化系统深度融合,核心由五大模块协同工作:
- 功能:将散装销子(直径 3-20mm,长度 10-50mm)通过振动排序,按 “大头朝前” 或 “小头朝前” 的统一姿态送入输送轨道(排序准确率≥99.5%);
- 优势:替代人工摆盘,单小时上料量达 3000-5000 件(是人工的 10 倍以上),且避免手部油污污染销子表面(影响加热均匀性)。
- 输送轨道:采用步进式输送,将销子逐一送至淬火工位(定位误差≤0.1mm);
- 专用夹具:气动夹爪精准抓取销子,确保其轴线与高频感应线圈同轴(偏差≤0.05mm),避免加热偏移。
- 线圈设计:根据销子形状定制(直杆销用环形线圈,台阶销用阶梯形线圈),确保加热区域精准(如仅淬火销子头部 3-5mm);
- 功率调节:PLC 根据销子材质(如 45# 钢、20Cr)自动调用预设功率(5-15kW),加热时间精确到 0.1 秒(确保温度稳定在 860±5℃)。
- 冷却系统:加热完成后,夹具带动销子立即进入喷淋区(冷却水压力 0.3MPa,流量恒定),冷却时间自动匹配加热参数(通常 3-5 秒);
- 下料轨道:冷却后的销子由夹具放入下料槽,自动流入收集箱(可区分合格 / 不合格品,通过在线硬度检测筛选)。
- 集成上料、加热、冷却、下料的时序控制,支持 100 + 种销子参数存储(换型时调用即可,无需重新调试);
- 实时显示生产数据(产量、合格率、设备状态),异常时自动停机报警(如缺料、水温过高)。
对比项 | 全自动淬火设备 | 人工 / 半自动淬火 |
---|
生产效率 | 单班(8 小时)产量 2-4 万件 | 单班产量≤5000 件(人工疲劳导致效率下降) |
质量一致性 | 硬度偏差≤±1HRC,合格率≥99.5% | 偏差 ±3-5HRC,合格率 85%-90% |
人工成本 | 1 人可监控 5-6 台设备,无需直接操作 | 1 台设备需 2 人轮换(上料、操作、下料) |
工艺追溯性 | 自动记录每根销子的淬火参数(温度、时间) | 无记录,质量问题无法追溯 |
某汽车零部件厂数据显示:采用全自动设备后,销子淬火的单位成本下降 30%(人工 + 废品率降低),且因质量稳定,下游装配线的故障率从 1.2% 降至 0.1%。
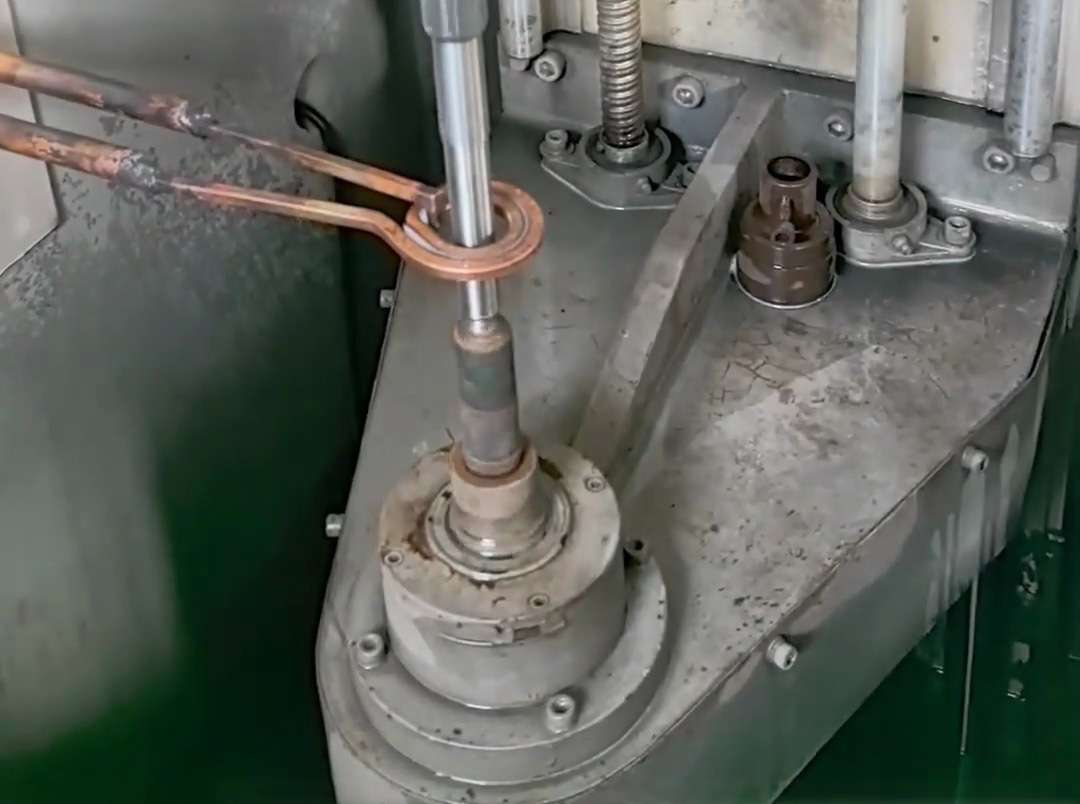
- 防错设计:振动盘内置缺料检测与卡料报警,若销子姿态异常(如歪斜),会被气动推杆自动剔除(避免进入淬火流程);
- 自适应调节:通过红外测温实时反馈销子温度,PLC 自动补偿功率(如环境温度变化时,加热时间微调 ±0.2 秒),确保温度稳定;
- 高频线圈耐用性:采用紫铜镀银线圈 + 水冷系统,连续工作 8 小时温度≤60℃,使用寿命达 50 万次以上(减少停机换线圈时间);
安全防护:设备全封闭设计,配备急停按钮、红外护手装置,符合 CE 安全标准(即使无人值守也无安全隐患)。
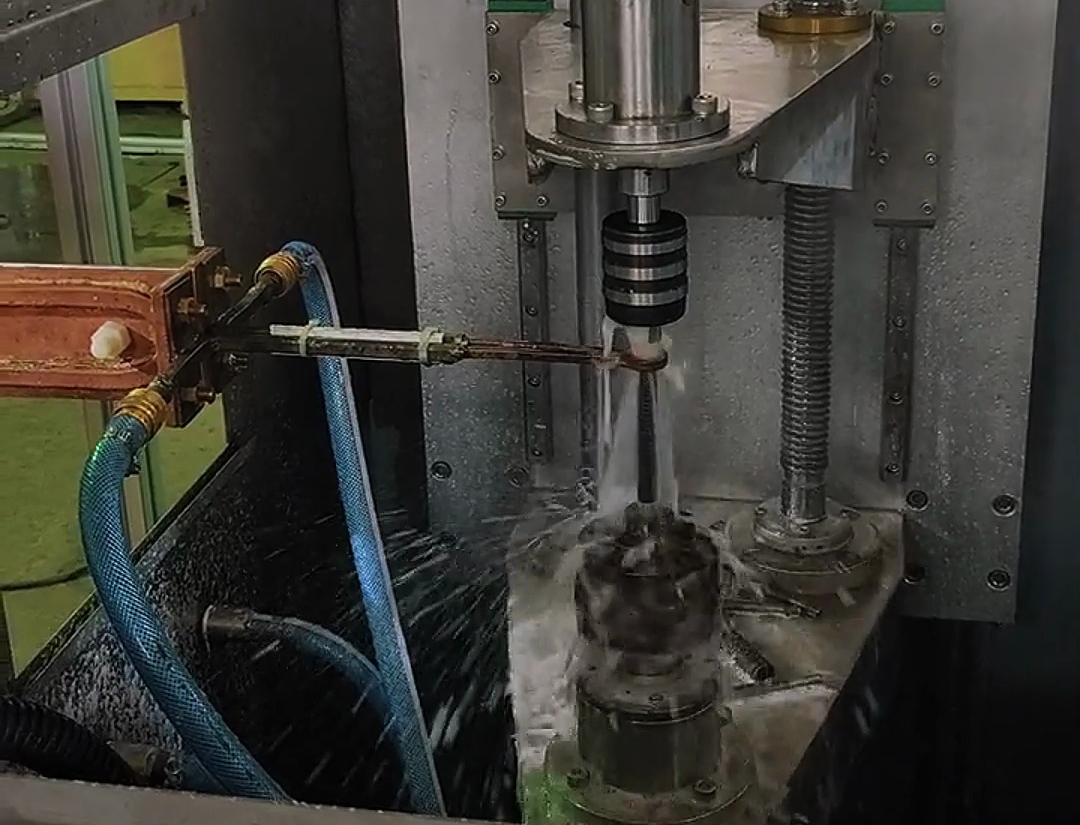
这套设备特别适合:
- 标准件厂的批量销子生产(如 GB/T 119 圆柱销、GB/T 117 圆锥销);
- 汽车、机械行业的定制化销子(如带孔销、台阶销)淬火;
- 可通过更换振动盘、夹具和线圈,快速适配不同规格销子(换型时间≤30 分钟),满足 “多品种、小批量” 柔性生产需求。
销子全自动高频淬火设备的出现,是热处理行业 “自动化 + 精密化” 的典型代表 —— 它将人工从重复性劳动中解放,同时通过程序控制实现了 “零误差” 生产。对于销子这类高批量、高一致性要求的零件,这种 “无人化” 不仅是效率的提升,更是质量标准的革命,为下游产业的稳定运行提供了坚实保障。