轴套高频淬火:表面强化与芯部韧性的平衡工艺
作者:
小编
点击数:
发布日期: 2025-07-15
轴套作为机械传动中的关键支撑部件(如轴承座、齿轮轴套),需在高负荷、高速旋转中承受持续摩擦与冲击,高频淬火通过 “表面局部硬化” 赋予其高耐磨性,同时保留芯部韧性,成为提升轴套使用寿命的核心工艺。
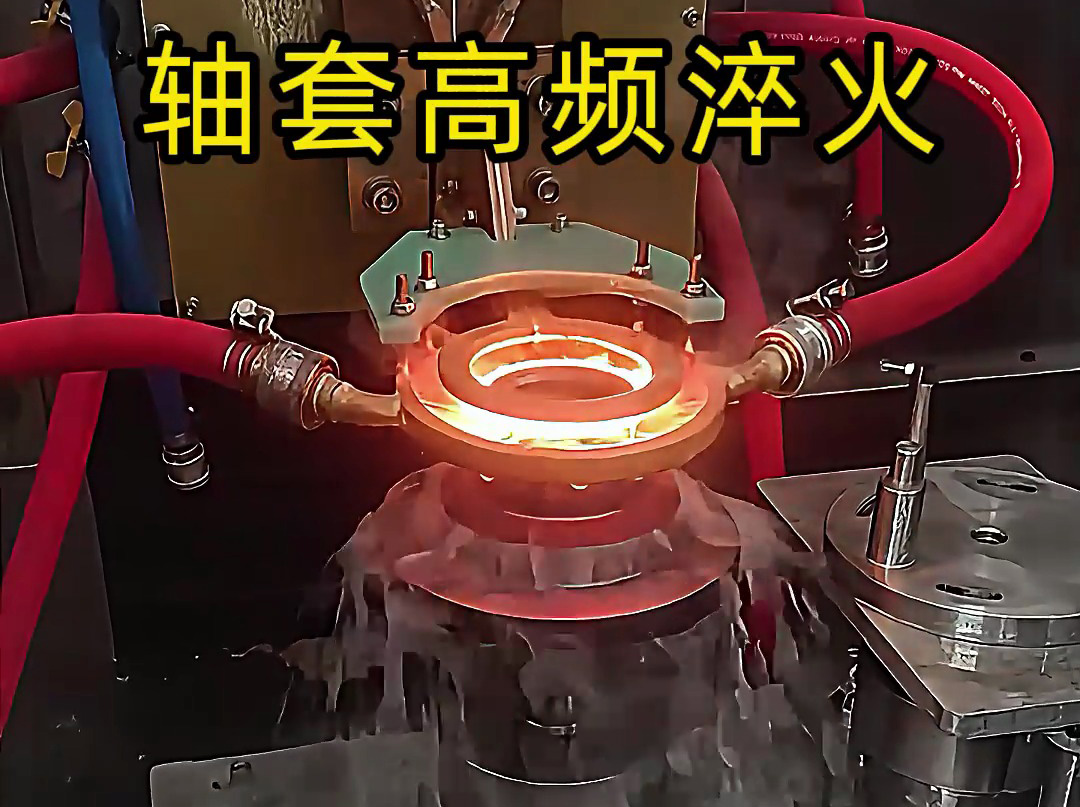
轴套在工作中,内表面与轴颈接触产生滑动或滚动摩擦(易磨损),外表面与座孔配合承受径向载荷(需抗冲击),高频淬火通过精准的 “表面 - 芯部” 性能设计实现适配:
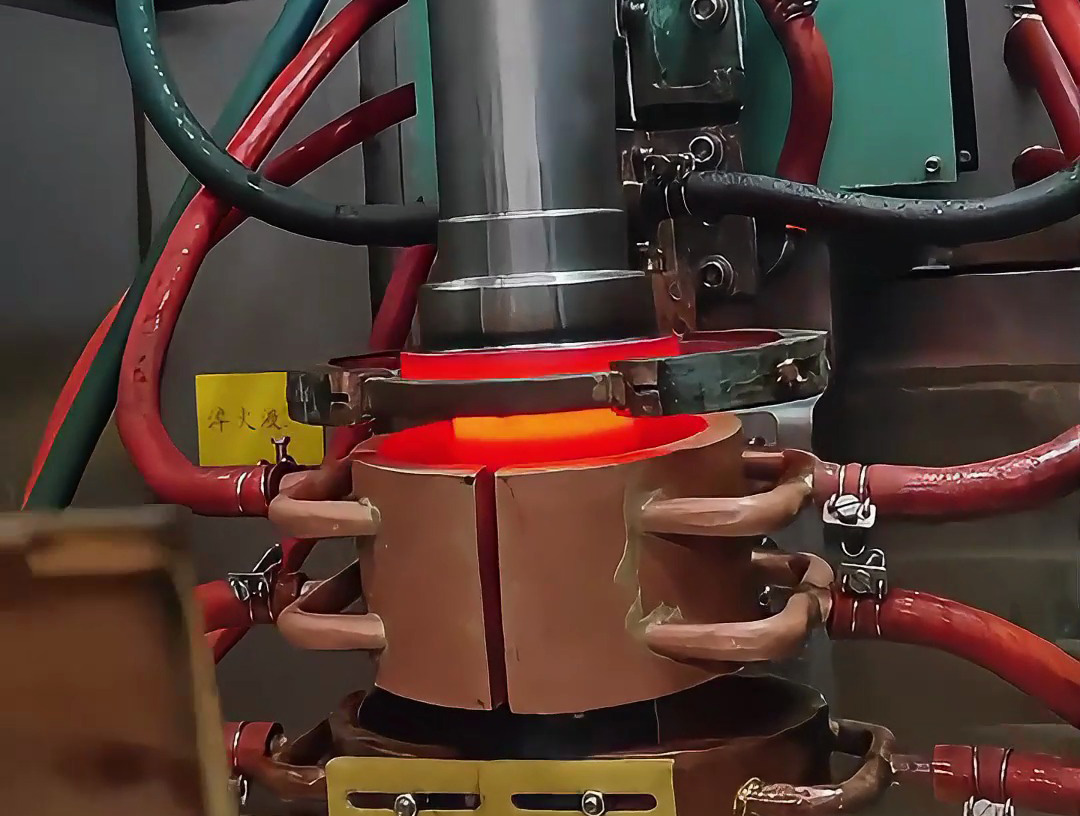
相比整体淬火或渗碳工艺,高频淬火在轴套处理中优势显著:
轴套多为薄壁圆筒结构(壁厚 5-20mm),整体加热易导致椭圆度超差(≥0.1mm),而高频淬火通过:
- 定制线圈:采用环形感应线圈,与轴套外圆(或内孔)保持 2-3mm 均匀间隙,确保圆周方向加热均匀;
- 快速冷却:加热后立即通过喷水环(内孔淬火)或外淋(外表面淬火)冷却,热影响区仅 3-5mm,轴套椭圆度误差≤0.03mm,无需后续校直即可装配。
- 短时加热:单件轴套(如 φ100×50mm)加热时间仅需 5-10 秒,配合自动上下料机构,每小时可处理 500-800 件,效率是渗碳工艺的 10 倍以上;
- 材料兼容:适配中碳钢(45#)、合金钢(40Cr)等常规材料,无需使用高价合金渗碳钢,原材料成本降低 15%-20%。
根据轴套受力特点,高频淬火可针对性强化关键区域:
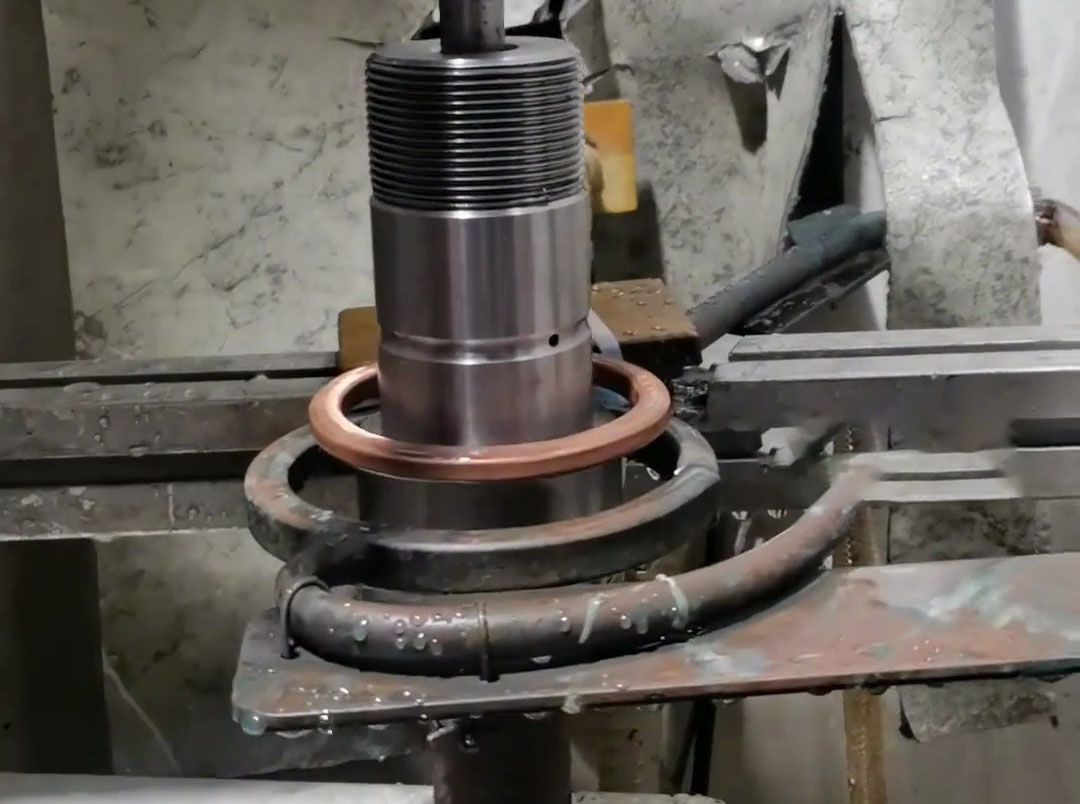
硬化层深度与均匀性
通过调整高频频率(20-100kHz)控制硬化层深度:频率高则层浅(0.5-1mm,适合薄壁轴套),频率低则层深(1-2mm,适合厚壁轴套),确保圆周方向硬化层偏差≤±0.1mm。
温度与冷却速度的精准匹配
轴套材料为 45# 钢时,加热温度需控制在 860±10℃(奥氏体化充分),冷却速度≥150℃/s(确保马氏体转变完全);若为 40Cr 合金钢,温度可提高至 880±10℃,以保证合金元素充分溶解。
开口轴套的特殊处理
对带开口槽的轴套(如剖分式轴套),需在开口处设置屏蔽块,避免局部过热导致的硬化层不均,确保开口两侧 5mm 内硬度与其他区域一致(偏差≤±2HRC)。
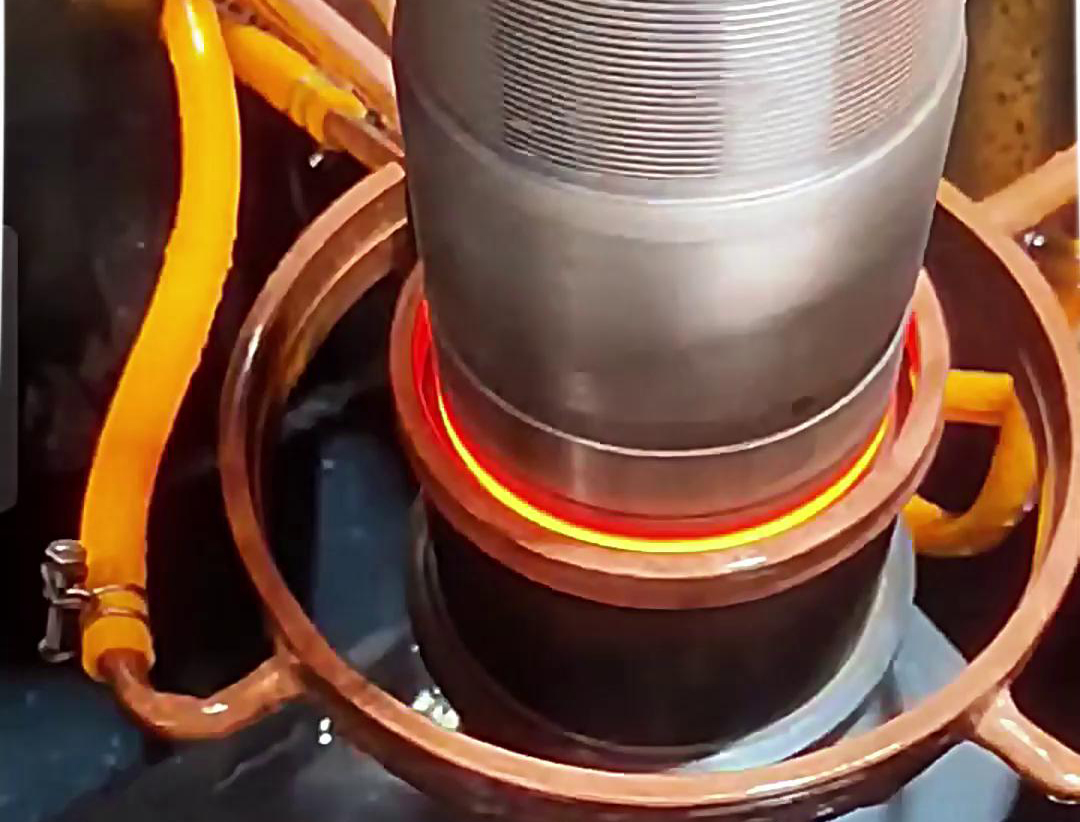
高频淬火后的轴套在多领域表现优异:
- 机床主轴轴套:内表面淬火后硬度达 HRC58-60,在转速 3000r/min 的切削工况下,磨损量≤0.01mm/100 小时,寿命是未淬火轴套的 3 倍;
- 汽车变速箱轴套:外表面淬火后抗冲击性提升,在换挡冲击载荷下(≥500N)无裂纹,疲劳寿命延长至 10 万公里以上;
- 液压油缸轴套:内孔淬火后表面粗糙度降至 Ra0.8,配合密封圈使用时,漏油率降低 90%,维护周期延长 2 倍。
轴套高频淬火通过对 “磨损区强化、非受力区保韧性” 的精准设计,完美平衡了轴套的 “耐磨性” 与 “抗冲击性”,其高效性与质量稳定性使其成为轴套制造中 “性能与成本平衡” 的首选工艺。对于高负荷、高频摩擦的轴套应用场景,高频淬火不仅是寿命保障,更是设备可靠运行的核心支撑。