数控高频淬火机床:精密热处理的 “智能利器”
作者:
小编
点击数:
发布日期: 2025-07-17
数控高频淬火机床融合数控技术(精准定位、程序控制)与高频感应加热技术(局部快速升温),实现金属工件表面淬火的 “高精度、自动化、高一致性”,成为机械制造、汽车工业等领域对零件表面硬度(如齿轮齿面、轴颈)有严苛要求的核心设备,其技术特性与应用价值深刻改变了传统热处理的工艺模式。
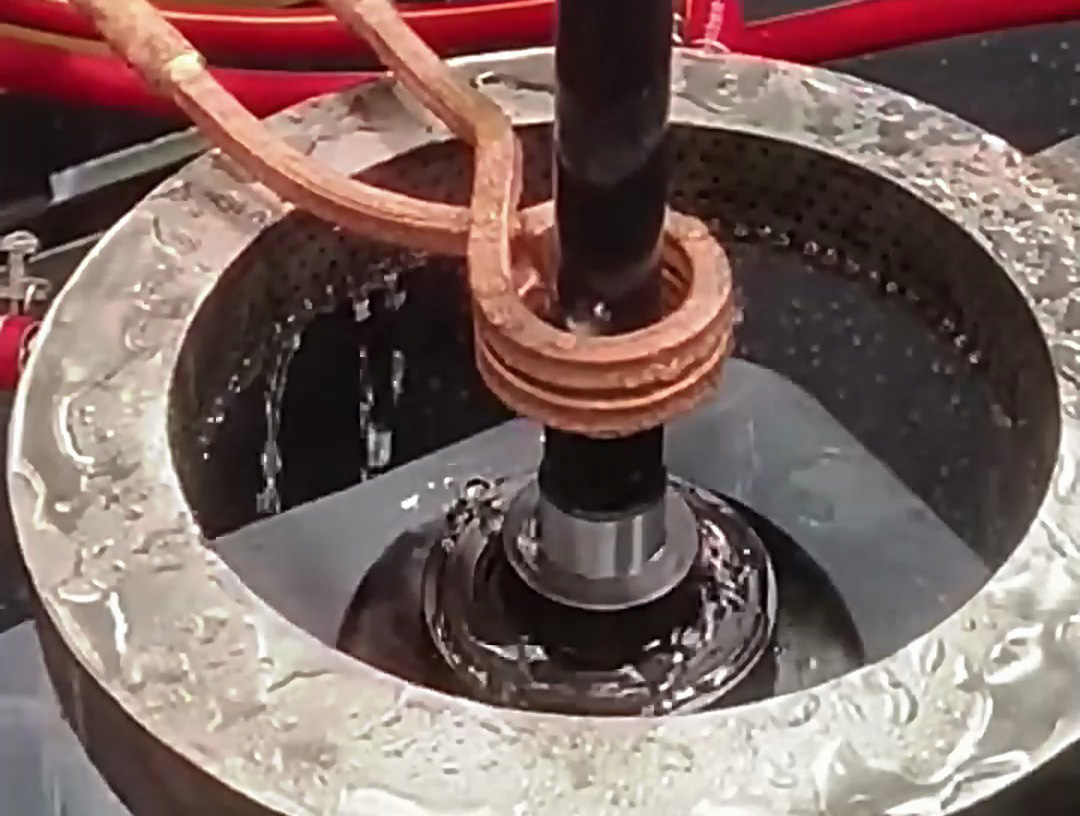
设备通过 “数控系统精准控制运动轨迹” 与 “高频模块精准输出能量” 的协同,破解了传统淬火 “定位不准、加热不均” 的痛点:
- 多轴联动控制:配备 X/Y/Z 轴伺服电机(部分含旋转轴 C 轴),定位精度达 ±0.01mm,确保感应线圈与工件淬火区(如齿轮齿面、轴颈台阶)的相对位置偏差≤0.02mm(避免局部过热或欠热);
- 自定义运动轨迹:通过 CAD 导入工件三维模型,自动生成线圈运动路径(如齿轮淬火时的仿齿形轨迹、长轴淬火时的螺旋线轨迹),支持 1000 + 套程序存储(调用时间≤3 秒),满足多品种工件快速换型;
- 实时反馈调节:激光位移传感器实时监测工件实际位置(补偿装夹误差),动态修正轨迹(响应时间≤0.1 秒),确保批量工件淬火一致性(合格率≥99%)。
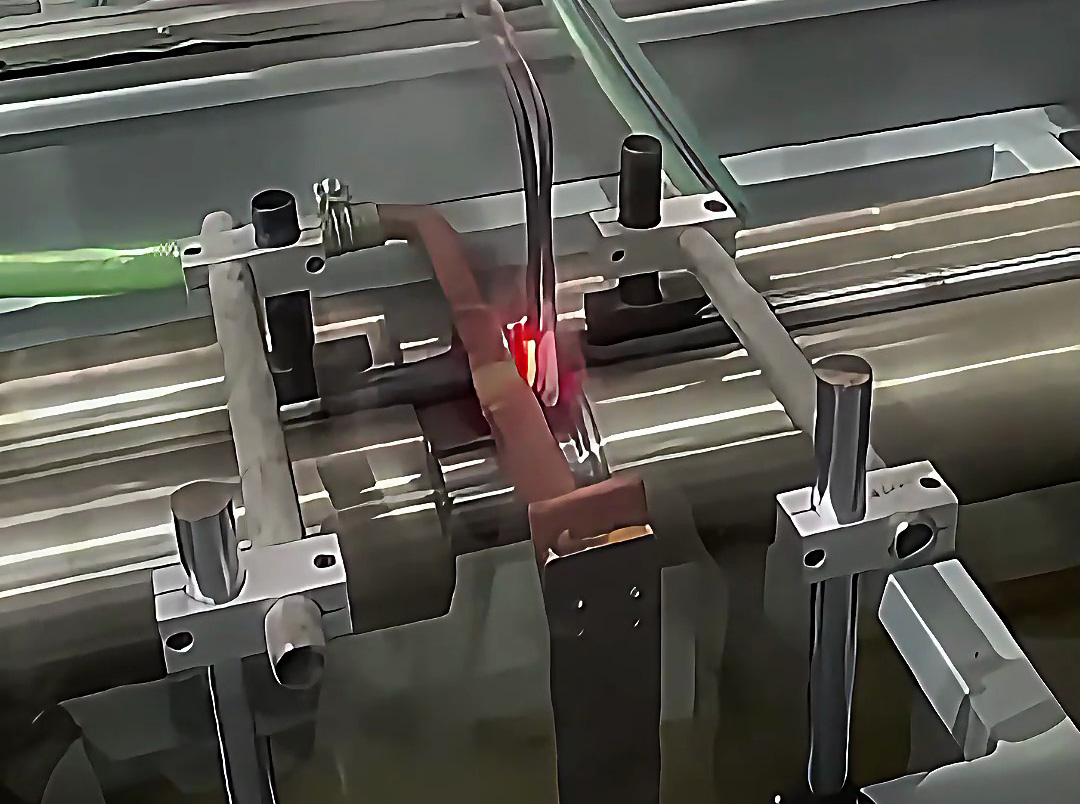
相比传统手动高频淬火或中频淬火,数控高频淬火机床的优势体现在多维度突破:
- 硬度均匀性:同一工件淬火区硬度偏差≤±1HRC(如齿轮齿面从齿顶到齿根硬度均为 HRC58±1),传统工艺偏差常达 ±3-5HRC;
- 硬化层一致性:深度偏差≤±0.1mm(如要求 2mm 硬化层,实际为 1.9-2.1mm),确保工件疲劳寿命稳定(如轴颈淬火后抗弯曲疲劳强度提升 40%);
- 变形量极小:局部加热 + 对称冷却使工件变形量≤0.05mm/m(如长 1 米的轴类淬火后弯曲度≤0.05mm),无需后续校直即可装配。
- 全流程无人干预:配合自动上下料机构(机械臂 / 传送带),实现 “上料→定位→加热→淬火→下料” 全自动,单班(8 小时)产能达 500-2000 件(如汽车变速箱齿轮),较人工操作提升 3-5 倍;
- 快速换型能力:更换工件时,仅需调用对应程序 + 更换线圈(10-15 分钟),支持 “多品种、小批量” 生产(最小批量 50 件),满足定制化制造需求。
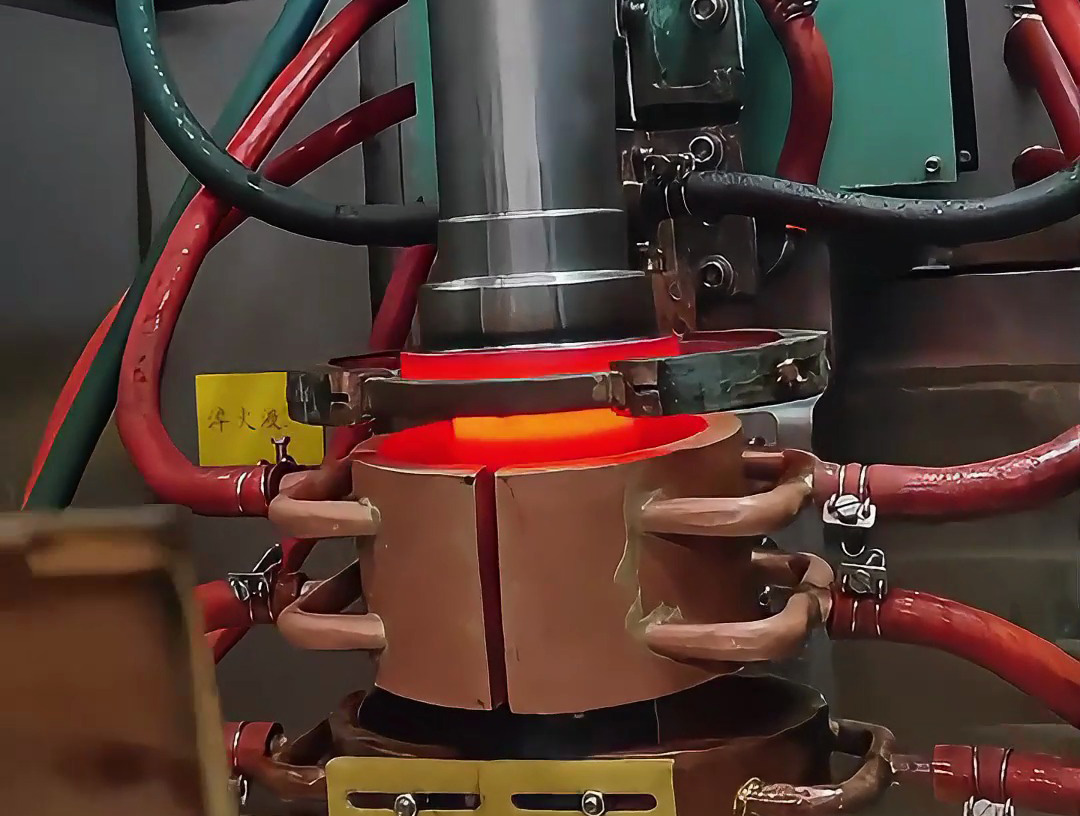
数控高频淬火机床的高精度特性,使其成为高要求领域的 “标配”:
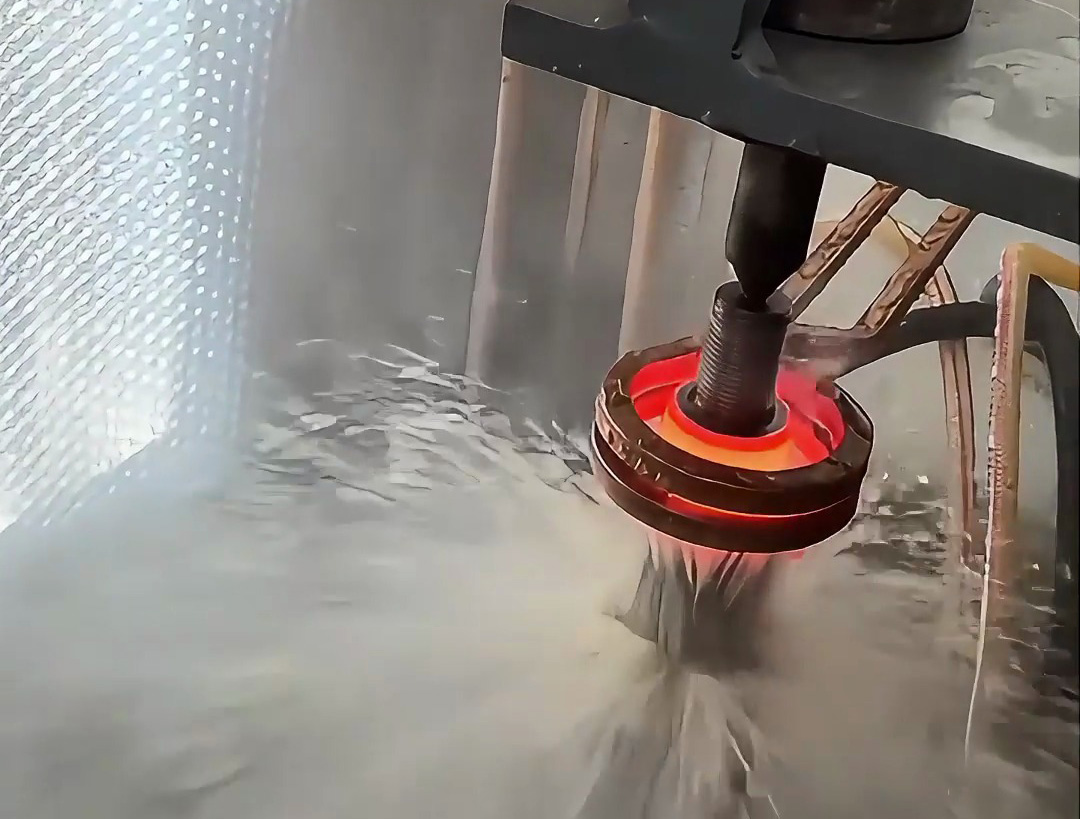
对比项 | 数控高频淬火机床 | 传统手动高频淬火机 | 箱式炉整体淬火 |
---|
精度控制 | 硬度偏差 ±1HRC,变形量≤0.05mm/m | 硬度偏差 ±3-5HRC,变形量≥0.1mm/m | 硬度偏差 ±5HRC,变形量大需校直 |
效率 | 全自动,单班产能 500-2000 件 | 人工上下料,单班产能≤200 件 | 批量处理,单炉需 2-4 小时 |
适用场景 | 高精度、多品种、小批量 | 低精度、单一品种、大批量 | 低精度、大型简单件 |
数控高频淬火机床的核心价值,在于将热处理从 “经验主导的手艺活” 升级为 “数字驱动的精密工艺”。通过数控技术与高频感应加热的深度融合,它不仅满足了现代工业对零件表面硬度、精度的严苛要求,更适配了 “柔性生产、快速响应” 的制造趋势,成为连接 “设计精度” 与 “实际性能” 的关键设备,推动热处理行业向 “智能化、高质量” 转型。