高频感应加热机加热铁钳:替代明火的高效安全解决方案
作者:
小编
点击数:
发布日期: 2025-07-17
铁钳(如钢丝钳、断线钳)的刃口淬火热处理需快速、局部升温至奥氏体化温度(850-900℃),高频感应加热机凭借 “高效、精准、安全” 的特性,完美解决明火加热(煤炉、气炉)的固有缺陷,成为铁钳热处理的优选方案,其技术优势与生产价值体现在多维度的全面升级。
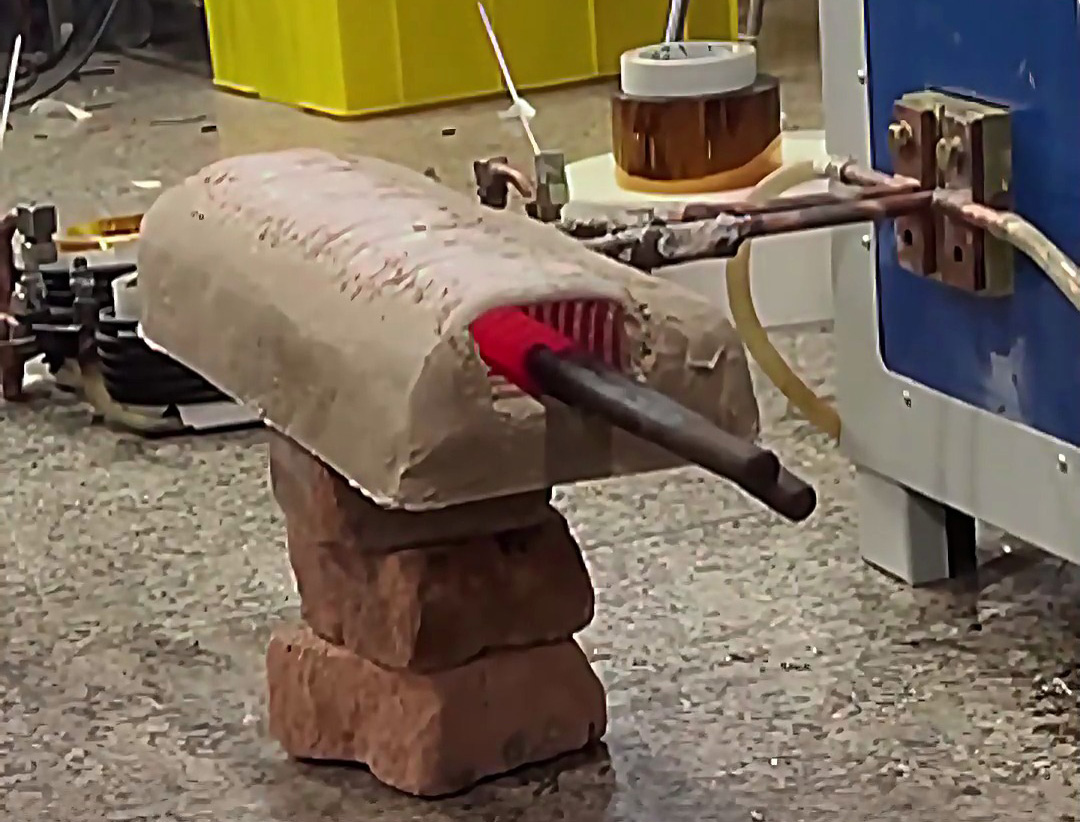
传统明火加热在铁钳处理中存在难以克服的问题,直接影响生产效率与产品质量:
加热效率低下,能耗浪费严重
煤炉、气炉通过火焰热辐射加热,热量需先加热空气再传递到铁钳,热损失率超 60%(仅 40% 以下热量被铁钳吸收)。一把铁钳(约 200g)加热至 900℃需 5-8 分钟,单炉次处理量有限(≤10 把),单班产能不足 500 把,远低于规模化生产需求。
温度失控,铁钳质量稳定性差
- 明火温度受燃料供应量、风力等因素影响,波动范围 ±100℃以上,易导致铁钳刃口 “过烧”(温度超 1000℃,晶粒粗大、脆性增加)或 “欠烧”(温度<800℃,淬火后硬度不足 HRC50);
- 加热不均匀,铁钳刃口与钳身温差大(刃口红热时,钳身已烫手),淬火后易因应力集中导致钳身开裂。
安全与环保隐患突出
- 明火作业存在火灾风险(尤其使用汽油、酒精助燃时),且煤气泄漏、煤炉一氧化碳中毒等安全事故频发;
- 燃烧产生大量烟尘(如煤炉的二氧化硫、气炉的氮氧化物),不符合现代车间环保标准(粉尘排放需≤10mg/m³),工人长期暴露易患呼吸道疾病。
依赖人工,劳动强度与成本双高
需熟练工人手持铁钳在火焰中翻转调整,凭经验判断加热火候(“看颜色定温度”),劳动强度大(高温环境 + 重复动作),且人工成本占比超 30%(单班需 2-3 人),人员流动还会导致产品质量波动。
高频感应加热机(频率 10-500kHz)通过电磁感应使铁钳自身生热,从原理上规避明火缺陷,实现铁钳加热的 “质效双升”:
秒级加热,效率提升 10 倍以上
高频电流通过感应线圈产生交变磁场,在铁钳刃口诱导涡流直接发热,热量转化率达 60%-70%(是明火的 1.5 倍以上)。一把铁钳刃口加热至 900℃仅需 3-5 秒,配合自动送料机构,单班产能可达 5000-8000 把,完全满足规模化生产需求。
精准控温,铁钳质量稳定性 99% 以上
- 配备红外测温仪与 PLC 控制系统,温度设定精度 ±3℃,实时反馈并调节功率(响应时间≤0.1 秒),确保每把铁钳刃口温度稳定在 850-900℃(淬火后硬度 HRC55-60,偏差≤±1HRC);
- 感应线圈按铁钳刃口形状定制(如 “U 型” 聚焦刃口),仅加热需淬火区域(钳身温度≤100℃),热影响区≤5mm,淬火后铁钳变形量(如刃口直线度)≤0.05mm,无需后续校直。
无明火污染,符合安全环保标准
- 全程电加热,无火焰、无烟尘,车间噪音≤60dB(远低于气炉的 85dB),工人劳动环境显著改善,符合 GB12348-2008 工业厂界环境噪声排放标准;
- 内置过温、过流、缺水保护(冷却水路异常时自动停机),无火灾、中毒风险,安全事故率降至 0.1‰以下。
自动化集成,大幅降低人工成本
可与振动盘上料、机械臂翻转、自动冷却机构组成生产线,工人仅需监控设备运行(1 人可看管 2-3 台机),人工成本降低 70%;且程序存储 100 + 种铁钳参数(如 “8 寸钢丝钳”“10 寸断线钳”),换型时调用程序 + 更换线圈(5 分钟内完成),适应多品种生产。
对比明火加热,高频感应加热机在铁钳处理中展现出 “效率、质量、安全、成本” 的全面优势:它不仅解决了明火的 “慢、差、险、贵” 问题,更通过自动化与精准化,推动铁钳热处理从 “粗放加工” 升级为 “精密制造”。对于五金工具企业而言,选择高频加热机不仅是工艺升级,更是降本增效、保障生产安全的 “战略选择”—— 毕竟,在规模化生产中,“稳定的质量 + 高效的产能” 才是核心竞争力。